 |
No.046 |
湿し水の選択について(2) |
2009/12 |
|
|
前回(No.41)コラムでは、どの湿し水を使うかという選択基準として、
- 使用している印刷機の給水機構に合った給湿液効率(FSE)(充分かつ、制御可能な水揚がりの実現)
- 使用インキと湿し水の適性な乳化(インキが湿し水に溶解することの無く、初期乳化が早く版面に転移後、インキから水滴が排出しやすいズリ乳化状態の実現)
- 非画線部の不感脂化修復性能(より薄い水膜で必要な不感脂化修復性能の実現)
の3点を挙ましたが、今回はこの3点の特性を維持させる為の複合、補助的な特性の1つとして『pH緩衝性能』について説明したいと思います。
pH緩衝作用とは『一部中和された弱酸と弱塩基(アルカリ)が水溶液中にあるとき、外部から 酸・塩基を加えてもpHが僅かしか変化しない状態』と定義されています。
新聞印刷などを除く、一般の平板印刷用の湿し水原液には、弱酸と弱塩基を配合し、使用濃度でpHが3.5〜5.0位になるように調製されます。そのpH領域で緩衝作用を発揮しますが、配合される弱酸と弱塩基の量が多ければ多いほど緩衝作用は強くなります。
弱酸性のpH域を逸脱しないようにする理由として、下記の3点が考えられます。
- 選択される酸自体に版面非画線部の不感脂化修復効果があり、その酸の効果と緩衝作用を同時に発揮させようと塩基と組み合わせると必然的に弱酸性になる。外的要因で湿し水のpHがアルカリ域にシフトすると、不感脂修復効果が弱まる
- 不感脂化剤として配合されるアラビアガムなどの水溶性ポリマーの機能が発揮すのが弱酸性の一定領域に限られる為
- 外的要因で湿し水のpHが適した領域外(アルカリ域、pH=3以下のより強い酸性域)にシフトするとインキとの乳化バランスがくずれる。
pH域をアルカリ側にシフトさせる要因として、使用水の硬度、炭酸カルシウムなどの印刷紙成分によるもの、インキの成分によるものが挙げられます。
特に使用濃度での湿し水成分の95〜99%は使用水ですので、その硬度の影響は大で、比較的硬度の高い地域(※総硬度100〜150)では、pHの変動を抑える為、pH緩衝性能の高い湿し水が必要になります。
※硬度とは
水の中に溶けているカルシウムイオンとマグネシウムイオンの量のことで、炭酸カルシウム(COCO3)が1L中に含まれているmg数で表します。WHO(World Health Organization:世界保健機構)の飲料水水質ガイドラインでは以下のように分類されています。
湿し水のpH緩衝性能はより高いほうが良いのですが、最初に挙げた湿し水選択基準3点の特性がバランス良く発揮させることを考えると、配合できる緩衝成分の量にも限界があり、pHをアルカリ側にシフトさせる要因が重なった場合、湿し水に緩衝剤を別添加したり、湿し水濾過装置(No.44 濾過装置導入のメリット 参照)によって、循環している湿し水よりインキ滓、紙粉などを除き、溶出するアルカリ成分の量を減らすことも有効な手段です。
また、水道水の硬度は、四季を通じて大なり小なり変化しますので、より安定的な印刷を実現する為に、使用水をイオン交換処理(純水装置)で水の硬度をゼロにして、常に一定の硬度で印刷をしている会社や、純水に硬度保証剤を硬度20〜50になるように添加して印刷をしている会社もあります。
|
|
|
|
|
 |
No.045 |
オフ輪の今後 |
2009/11 |
|
|
〜その1〜
印刷会社の倒産が相次いでいます。
冒頭からネガティブな内容で申し訳ないのですが、これが印刷業界の現状です。
東京商況リサーチによると、2009年上半期(1月〜6月)の全国企業倒産件数(負債額1,000万円以上)は8,169件、負債総額が4兆6,853億 3,600万円。倒産件数は、前年同期比625件増(8.2%増)、負債総額は前年同期3,179,677百万円(+47.3%)とあります。印刷業の 2009年上半期の倒産(こちらは帝国データバンク調べ)は89件。前年同期比61.8%の大幅増加で2001年以降最多となるそうです。国内企業全体が不況の只中にありますが、印刷業界は倒産件数の増加率を見ても深刻な状況です。特にオフ輪会社の厳しい現状が自分の耳にも届いています。今年に入り、倒産、或いはオフ輪部門のみ閉鎖した会社は多くあります。
しかし、そこで悲観ばかりはしていられません。現実は現実として受け止め、何故そうなったのか?今後どうしてくべきなのか?ということも真剣に考えなくてならないでしょう。数回に分け、オフ輪業界の現状・今後について書いていきたいと思います。
まず、はじめにオフ輪機台数の推移です。尚、これは商業・出版用オフ輪機のみのデータで、新聞輪転機は含まれません(日本印刷新聞社調べ)
1999年 1461台
2005年 1327台
2007年 1402台
2008年 1289台
内訳はB2版が約62%、A1版が約18%で、残り20%がB3機などです。A1機のシェアは拡大傾向にあります。
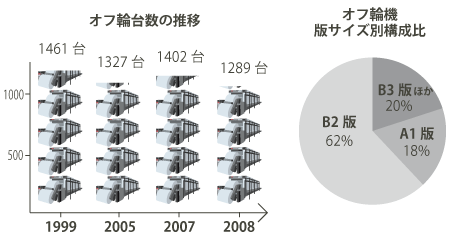
この調査は回答制で、中には回答を辞退した会社もあるようなので、実態と完全に一致してはいませんが、概ねの傾向は表れていると思います。
近年では1999年がピークで、オフ輪業界に不況の兆しが見え始めたのはこの頃です。1999年当時、自分はまだオフ輪機のオペレーターを務めており、ちょうどこの頃から、社内でも経費削減対策などが増え始めました。自分もまだ気楽に構えていた時期なので「いちいちうるさいなぁ」などと感じていた記憶があります。
新台設置の理由には、以下のようなことが挙げられます。
- 従来機が老朽化したため
オフ輪機が新聞折込チラシの一般的生産設備として使われ始めたのは、1970年代に入ってからで、この時期から1980年代にオフ輪機は一気に増加しました。この期間に導入されたオフ輪機の入れ替え(引退)時期が、2005年前後に重なったためと予想できます。
- 印刷品質の向上
従来、短納期・大ロッドが主目的だったオフ輪印刷に、枚葉水準の品質が求められるようになりました。印刷機械の進化により、それに近い精度も実現可能になっています。オフ輪各社が品質で他社に負けないためには、新台の導入に踏み切る必要がありました。@はこの理由とも重複します。
- 付加価値印刷
国内経済が悪化し、印刷業界にもデフレの波が押し寄せました。単価の値下げ合戦が続き、これ以上の値下げは厳しい状況まで達した結果、価格以外で他社との差を付けるため、様々な折加工やシート印刷が可能な新台に注目が集まります。それまで主流だったB2機からA1機にシフトチェンジする会社が増えたのも同様の理由です。
推測も含みますが、上記のような理由で、オフ輪機は一時的に増加しました。しかし、景気悪化の波には逆らえず、倒産・閉鎖に至るオフ輪会社が増加していきます。 また、印刷機台数のデータだけでは読み取れない事実が1つあります。それは印刷機械の高速化です。
インターネットやデジタル印刷の普及により、オフセットでの印刷物総数は減少傾向にあります。それに反比例するように、オフ輪機の回転速度は高速化していきました。自分がオフ輪オペレーターだった1990年代後半は、BT半裁機で毎時30,000〜35,000部程度が平均的な印刷速度でした。ところが最近は、毎時48,000部程度の印刷が可能になっています。これを人間の100m走に例えると、10秒フラットで走っていた人が6秒25で走ることになるのですから恐るべき進化です。ボルトでも到底不可能でしょう。この結果、印刷作業がさらに短時間で済むようになり、全国的に機械余りの状況を生み出してしまいました。
各社は他社との差別化を図るために新しい印刷機を導入したのですが、皮肉にも、それが印刷機械をダブつかせることに繋がり、倒産・閉鎖に至る企業が増えてしまいました。
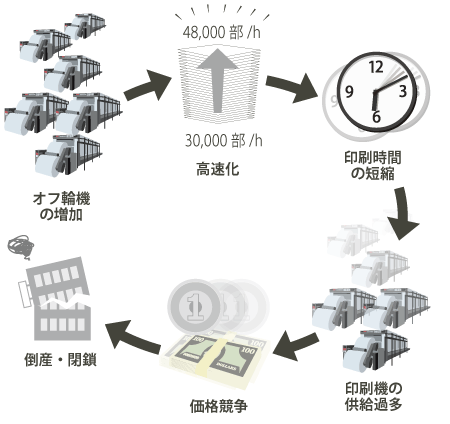
これが、現在のオフ輪業界の現状です。
しかし、ネガティブにばかり捉えているわけにはいきません。これまでの状況を的確に把握し、現状を打破する方針を今後も考えていくべきでしょう。
次回は、諸外国のオフ輪業界との比較から、日本のオフ輪業界の今後を考察していきたいと思います。
|
|
|
|
|
 |
No.044 |
濾過装置導入のメリット |
2009/10 |
|
|
湿し水は、別名「印刷の血液」と呼ばれるほど、印刷において非常に重要な役割を担っています。湿し水が不安定な状態になれば印刷品質も不安定になりますので、高品質な印刷を維持するためには、湿し水の管理を最優先に行う必要があります。
湿し水は時間の経過とともに、インキ・用紙・パウダー等の成分が混入し、徐々に劣化をしていきます。特に最近では、用紙から受ける影響がとても大きくなっており、湿し水の劣化は従来よりも激しいものとなっています。湿し水が劣化していくと水上がりが不安定になり、汚れや過乳化、さらにはローラーに対するカルシウム付着等の悪影響を及ぼします。
湿し水の劣化を防ぐことは不可能ですが、濾過装置を使用して劣化を遅らせることは可能です。従来は湿し水が劣化した場合は水交換をすることで解決していましたが、濾過装置を使用すれば湿し水の交換頻度を以前よりも減らすことが可能になります。
濾過装置とは、その名の通り湿し水を濾過フィルターに通すことで、湿し水に含まれた不純物を取り除き、湿し水の劣化を大幅に遅らせる働きをします。
例えば、これまで2週間に1度のペースで交換していた湿し水を、3ヶ月前後に引き伸ばせるようになります。これは単純に水交換の頻度を減らすだけでなく、湿し水の外的要因による変動を抑え、湿し水の劣化を最小限に食いめ、結果として湿し水の安定化と印刷の安定化を図ることができます。
これらの効果だけでも十分メリットのある濾過装置ですが、実はそれだけではありません。濾過装置の導入には、印刷現場で一番の課題となるコストに関しても大きなメリットを生む可能性があります。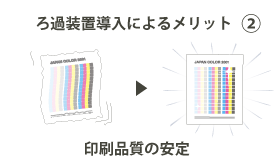
水交換とは、古い湿し水を捨てて新液を作る作業です。新液を作るためにはH液やIPAを必ず添加するので、水交換の度にそれらを消費することになります。この作業にかかるコストは目立ちにくいですが侮れない金額になります。
具体的な金額は、湿し水タンクの容量・H液の添加量・H液の購入金額・水交換の頻度によって決まりますが、あるお客様で調べたところ1台の機械で年間30万円以上の費用が水交換で発生していることが見える化された例もあります。
このような場合、濾過装置を導入し水交換の回数を減らすことで大幅なコスト削減が可能になります。実際には濾過装置の導入コストがありますので、導入から数年間は機械代金の償却と考えますが、それが済んでしまえば純粋なコストメリットとなります。
このように、濾過装置は湿し水の状態を維持し印刷品質を守るだけでなく、コスト面においても貢献度の高い装置といえます。
濾過装置の導入を検討されている印刷会社様がおりましたら、湿し水のチェックから試算表の作成、さらには安心の2ヶ月導入テストまで弊社で対応することが可能です。この機会に是非お問い合わせをお待ちしております。
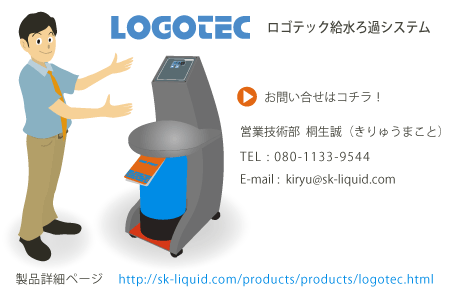
|
|
|
|
|
 |
No.043 |
マイスター制度 |
2009/09 |
|
|
No.040のコラムで弊社の桐生が印刷技能検定に関して書いているが、今回は印刷発祥の地ドイツでのマイスター制度に関して説明しようと思う。
マイスター制度は、手作業による仕事の伝統を維持し、そのレベルを保持し後継者を育てるための制度で、中世以来の伝統を持ち、1953年からは職能制度として法制化されて、ドイツの産業発展に大きな役割を果たしてきたとされている。ドイツの印刷業界もこの制度下のもとに発展し、現在の世界を牽引する印刷業界があるのだと思う。
マイスター取得までの経緯を簡単に説明すると、まずは見習い工として3年働きながら職業学校に通い、さらに「徒弟」(Geselle)として3〜5年の修行を積んだ上で、試験に合格するとマイスターの資格が取得できる。
従来ドイツの法律では、各職業においてマイスターの資格がなければ開業ができないとされてきたが、現在では多くの職業でマイスターでなくとも開業ができるように法律が改正されている。しかし、マイスターの資格取得そのものは現在でも存在していて、多くの若者が自分の進むべき職業でマイスターの資格を取得して、誇り高き職人として社会人生活を送っている。
先日ヨーロッパ諸国の印刷会社を訪問する機会があり、ドイツ・スイスの印刷会社を訪問してきたが、どの会社の機長または現場責任者も、自分達の仕事に対して強いプライドと責任感を持ち合わせていることが感じ取れた。
日本にも印刷技能検定という制度があるが、残念ながらドイツのマイスター制と社会的地位を比較すると、決して認められているとは感じられない。
今後日本の印刷業界及び印刷現場が更なる飛躍を遂げるには、日本の印刷技能検定の重要性を業界全体で高めていく必要があるのではないだろうか。誇り高き印刷オペレーターが日本の印刷会社と印刷業界を支える。そのような姿を実現させたいものだ。 |
|
|
|
|
 |
No.042 |
バケーション |
2009/07 |
|
|
7月に入り、各国の取引会社からバケーションのお知らせが舞い込んできている。
ヨーロッパの企業は8月に1週間〜2週間会社全体を閉めてしまうケースが多い。過去には3週間も閉めてしまう会社もあったが、最近は2週間が一般的だ。
それに対して当社はお盆前の2日間。
「いやー、日本人は勤勉だなー!偉い偉い!」と誇りに思うのと同時に、「いや、働きすぎかな?」と毎年疑問に思う時期である。
人生は一度きり。その人生を謳歌するのが我々の目的であるべきだが、とかく日本人は仕事に追われてプライベートがおろそかになりがちだ。
昨今の不況の中で、売上!利益!経費削減!と毎日仕事のペースを上げて、汗を流して働いているのが現在の我々である。
しかしアメリカの独立宣言にあるとおり、人間が目指すものは幸福の追求であり、お金の追求ではない。
日本人はその事に気付いた方がより良い人生が送れるのでは?
時には仕事を忘れてじっくりと休む。
日本にもバケーションと呼べる位の長期休暇がとれる時代が来ると良いですねー。
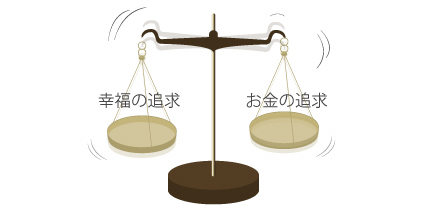
|
|
|
|
|
 |
No.041 |
湿し水の選択について |
2009/06 |
|
|
ここ数年の印刷業界では、環境問題、労働安全性や各種法規制による社会的ニーズの高まりからインキメーカー、湿し水メーカーによるIPAを使用しない湿し水の製品開発が進められてきました。多くの製品が市場に投入、評価され、ノンIPA化を実現している印刷会社も増えてきました。実際ノンIPA化を実現しているところでは環境問題、労働安全性もさることながら、印刷品質の向上、経費削減にも役立っていることを良く聞きます。
ノンIPA化を実現にあたって、どのメーカーのどの湿し水の使うかということは重要な選択ですが、下記3点の湿し水の特性が自社の印刷環境で十分に発揮できるかが選択基準になると思います。印刷環境とは自社で使用中の印刷機の種類とコンデション(版、ローラ、ブランケット材質も含む)、水(水質)、インキ(種類とメーカー)のことです。
- 高い給湿液効率(FSE)
- インキと湿し水の乳化適性
- 非画線部の不感脂化
高い給湿液効率は水揚がりの制御を容易にしますが、いかに効率良く水が揚がっても、インキと湿し水で適性な乳化が起こらず、 湿し水成分がインキ成分を溶解させたり、不可逆的な過剰乳化を起こしたり、また乳化が足りなく水量を増やしたりすると、水棒の絡み、地汚れ、つぼあがりなどの諸問題が発生してしまいます。
ここでいう適性な乳化とはインキと湿し水がローラー間を通過する際のズリ力によって、インキの版面への転移に必要な最低量の湿し水が水滴状になってインキ中に均質に分散し、版面に転移したのちは、より短時間でインキから湿し水が分離、しみ出すことが理想とされる可逆的乳化状態のことです。
現在、各社から販売されている湿し水は、機上でやや乳化抑制に働く配合が多いようです。非画線部の不感脂化ついては湿し水の基本特性として言うまでもありませんが、印刷物の乾燥性から、版の材質に合わせて、より薄い水膜で特性を発揮させることが重要です。
それぞれの印刷環境において、際立って印刷機のコンデションが悪いということがなければ3点がバランスが良く特性が発揮できる湿し水の選択で、いわゆる『水が絞れている』という水の送り量の調整が可能な状況になり(湿し水濃度1.5〜4%)、印刷品質を維持、向上、ノンIPA化の実現を容易にするもの考えています。
他にも湿し水に要求される特性として『pH緩衝性能』、『印刷機、版の腐食防止性能』、『湿し水の防腐性能』、『消泡性能』などがあります。前記3点の特性を維持させる為の複合、補助的な特性として重要ですが、詳細は別の機会に述べたいと思います。
弊社では昨年末から『SK-1』『SK-1N』『SK-1BF』という湿し水を開発、上市しており、多くのお客様でノンIPA化を実現していますが、今後もお客様の湿し水選択の幅を広げる為、特徴あるシリーズ製品を開発していく予定です。
もし弊社の湿し水を試用していただけるのであれば、事前に調査させていただく印刷環境から、ノンIPA化に向けての湿し水の選択、機械の調整をさせて頂くこともできますし、場合によっては湿し水配合のカスタムメイドも可能です。
ご希望の場合はお気軽にお問い合わせください。
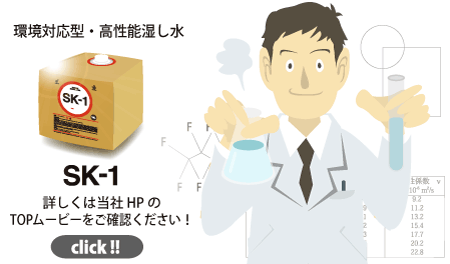
|
|
|
|
|
 |
No.040 |
技能検定 |
2009/05 |
|
|
技能検定というものを皆さんはご存知でしょうか?
技能検定とは「働く人々の有する技能を一定の基準により検定し、国として証明する国家検定制度」のことで、現在は125の職種について検定が行われており、これに合格することで国から資格が与えられる制度のことです。
我々の属する印刷業界ではオフセット枚葉印刷機を用いた検定が行われます。同じ印刷でもグラビア印刷やフレキソ印刷などのオフセット印刷以外では検定が行われていません。
印刷の検定は1級と2級に分れており、1級は4色機、2級は2色機を使用しての試験となり、それぞれ決められた課題をクリアしなければなりません。もちろんこの検定には学科試験もあり、学科を合格した人のみが実務試験に進むことができます。ですから、この検定に合格するためには印刷技術だけでなく、印刷に関わる基礎知識の把握も求められます。問題の中には日々の作業では学べないような内容も含まれていますので、過去問題などの参考書を用いて勉強する必要があります。
この技能検定を受けるチャンスは年に1度しかないので、合格出来なかった場合は1年後の検定を待つようになってしまいます。ただ、学科は合格したものの実務で不合格だった場合には次回以降の学科試験は免除されます。
注意点としては、この検定は実際の印刷機を使用するため受講出来る人数の枠がとても少なく、受講したくてもできないというケースが多くあるようです。特に1級の受講に関しては条件が厳しく、自社の印刷機設備を用いての受講が基本となります。つまり自分が所属する印刷会社の協力があって初めて受講が可能になるので、会社が協力してくれない場合や印刷会社に所属していない人は受講できないということになります。しかし、自分が調べた中で東京都だけは、印刷機メーカーや印刷学校などの機械を使うことができるので、 機械の提供なしでも1級の受講は可能となっています。それでも人数の制限はとても厳しく、申し込み開始日の職業能力センターには早朝から長蛇の列ができていて、実際に受講出来るのはその中でもわずかな人数のようです。
ちなみに受講する都道府県はどこを選んでも構わないので、1級を受講したい場合には東京都で受講することをお勧めします。
技能検定は、これまで現場で培ってきた技術や経験を計るためには最適な場だと思います。また、印刷技能士としての資格を得ることで、これまで以上に印刷に対する興味や責任感が沸いてくるのではないかと思います。
この資格については僕自身も取得を目指し勉強をしています。これを読んでくださっているオペレーターの方々も、一緒にチャレンジしてみてはいかがでしょうか?
http://www.javada.or.jp/jigyou/gino/giken.html
|
|
|
|
|
 |
No.039 |
枚葉とオフ輪の違い(3)
|
2009/04 |
|
|
今回はメンテナンスの違いについて触れてみます。
筆者はオフ輪出身なので、オフ輪を主眼に置いて書かせてもらっていますが、今回はオフ輪従事者には耳の痛い話です。
ローラー配列等、オフ輪・枚葉で機械構造の違いは色々ありますが、メンテナンス方法に大きな違いはありません。あるのはメンテナンスに対する意識の違いです。ハッキリ言ってしまうと「オフ輪会社(オペレーター)の方が、メンテナンスに対する意識が低い」ということです。
あくまでも個人的な意見ではありますが、営業として多くの印刷会社を廻らせてもらった上での認識なので、傾向としては間違っていないはずです。例えば、ローラー洗浄ひとつ取ってみても、枚葉各社からは、洗浄剤や洗浄法の問い合わせを頻繁に受けますが、オフ輪会社からは顕著に少ないと言わざるを得ません。オフ輪会社の機械裏側に廻ってみると、床は油でベトベト、H液やシリコンの定量装置が壊れているため目分量で入れているというような光景も、決して珍しいものではありません。そういう自分も元はオフ輪のオペレーターです。現役当時は、さして変わらない作業状態でした。言うならば、オフ輪業界の悪しき習慣と言えるかもしれません(勿論、うちはそのようなレベルではない!という方も当然いらっしゃるとは思いますが、こういった会社もまだまだ多いという認識で読み進めて下さい)。
何故、オフ輪会社の方が、メンテナンスに対する意識が低いのでしょうか?
自分は以下の点が大きな要因になっていると考えます。
- チラシ印刷が多い
- 切り替え(色替え)が少ない
- 機械がデカい!
では、ひとつひとつ分析してみましょう。
- チラシはオフ輪業界で最も大きなシェアを占める仕事です(余談ですが、新聞の折込チラシは日本固有の文化だそうです)。チラシというのは、スーパーの特売日の広告に代表されるように「○月○日○時オープン!」などと「日時」が明確になっているものが多いため、下版した当日に輪転機を廻して30万部印刷。印刷が終了したら即断裁、真夜中にトラックで納品などということが日常的に行なわれています。つまり 「超短納期」なのです。その結果「とにかく刷る、とにかく間に合わせる」
ことが最重要視され、品質面への意識は薄れてしまっています。実際、印刷中に「色がうまく出ない」などの問題があっても、納期が迫っているため応急処置的な対策だけで仕事を進めてしまうことも多々あります。その仕事が終わっても、次の超短納期仕事が控えているため、メンテに時間を割けないままでいたりします。
- オフ輪はプロセスインキ(KCMY)がメインで色替え作業がほとんどありません。印刷用紙も斤量が違うだけで紙幅の変更が少ないため、多くの仕事は版交換のみで進行していきます。つまり、ローラー・インキ壷の洗浄作業が少なく、ブランケットのエッジマークや端汚れもそれ程気にしなくて良いということに繋がります。普段から小まめにローラーや壷・ブランケットを洗浄している枚葉オペレーターと比べると、それに対する意識が圧倒的に小さいのです。チラシ専門の印刷会社では、ローラー洗浄、壷のインキの入れ替えを
ほとんど行なわない会社もあるくらいです。結果として、ローラーにはグレーズが蓄積し、インキキーにはインキの塊が固着し、品質トラブルに繋がるということになるのですが…
- 機械が大きいと、人は「とても手が出せない」と思いがちです。例えば、車のバッテリーなどは結構簡単に交換出来るのですが、特に挑戦もせず最初から修理屋さんに依頼する人が多いのもそのためだと思います。オフ輪機の場合も同様の心理が働くようで、ちょっとした故障でも、
最初から機械メーカーに丸投げしてしまう会社がまだまだ多いようです。日常的にメーカーに依存することで、オペレーターの仕事は【印刷機を廻すこと】だけになってしまい、メンテナンスに気を配れなくなる傾向があるようです。
印刷機の進化に伴い、どんな作業体制でも、それなりの印刷品質が維持出来る時代になりました。その反面、顧客の要求は年々厳しくなり、最近ではオフ輪印刷にも枚葉美術印刷レベルの品質が求められるようになっています。メンテナンスの重要性については、これまでのコラムにも掲載してきたので、ここでは省力させていただきますが、印刷機の性能が横並びの現代に於いて、顧客の要求に応え、他社との差別化を図るには、日頃からのメンテナンスの徹底が第一です。オフ輪の仕事が激減して、印刷機の停止する時間が大幅に増えている今日、これを逆に良い機会と捉え、これまで実行されていなかった機械メンテナンスに時間を充ててみてはいかがでしょうか?機械いじりに慣れることで、きっと想像以上に自分達で出来ること、印刷品質向上に繋がることを発見できると思いますよ。
|
|
|
|
|
 |
No.038 |
ノンIPA化の薦め |
2009/02 |
|
|
年々、印刷業界では環境対策に取り組む企業が増加の一途をたどっています。その代表的な取り組みの一つに「IPAの削減」が挙げられます。既に取り組んでいる会社も増えてきていますが、全国の印刷会社を訪問して実情を目にする限りでは、まだまだIPAを使用している会社が数多く存在しているというのが率直な感想です。
私も長年印刷に従事してきて、IPAの特長と、「魔法の添加剤」とも呼ばれる効果は十分理解しております。しかし、その反面で環境規制の対象物質であること。そして環境と人体に与える悪影響が大きいということを同様に理解していただき、全国の印刷会社の皆様には是非ノンIPA化を目指してほしいと思います。
以下にIPAの特長を簡単に記します。
- 増粘効果: IPAは60%の添加率までは粘度が上昇するという特性を持ちます。そのため、添加することで湿し水の粘度が増し、給水ローラー間のニップをより効果的に移動し、版面への供給量が増えることになり、より効果的に非画線部の汚れを防止出来ることになります。
- 表面張力低減: この10年で印刷機のスピードはどんどん高速になり、それに伴い給水ローラーも高速で回転するようになりました。このような条件下でローラー表面と版面上に均一に湿し水を供給するためには、分子量が小さく表面配向能の高い物質が必要になり、IPAは非常に優れた効果を発揮します。
- 乳化制御効果: 基本的にインキと湿し水の乳化によって、紙に印刷が施されます。乳化率の低いインキと湿し水の組み合わせでは非画線部の水の供給が不足し、汚れの原因になります。逆に乳化率の高いインキと湿し水の組み合わせではインキの転移不良やローラーストリッピングなどを引き起こします。IPAはインキの乳化を抑制し、より印刷を安定させる効果を持ちます。
さて、最近では環境対策の一環として「ノンIPA化」が図れる湿し水原液が各メーカーより市販されています。しかし、その様なH液に変更したからといって簡単にノンIPA化が実現できる訳ではありません。ノンIPA化を実現するには幾つかのポイントがあり、その点をしっかりと押さえないと失敗に終わるケースがほとんどです。特にUV印刷においてのノンIPA化は、油性印刷と比べて非常に難しいと言えます。
それでもノンIPA化を勧める理由は、最初に述べた「環境と人体に与える悪影響」、「年々上昇傾向にある印刷資材のコスト削減」、それともう一つ強調したいのが、「印刷技術のレベルアップ」という点で大変有意義な試みだからです。
IPAを使用すると多少印刷機の調整が狂っても大きく印刷品質には影響しませんが、ノンIPAの場合は、それが顕著に印刷に出てきてしまいます。つまり、ノンIPAでの印刷は、より高いレベルでのマシンメンテナンスに対するスキルが必要とされるため、自然に社内の印刷技術のレベルアップにも繋がるという利点があるのです。
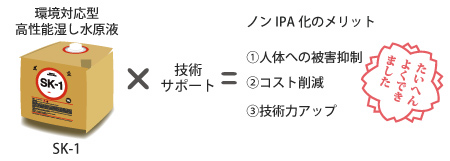
私どもエスケー液製造では、お客様の「ノンIPA化」を効果的にサポートするべく、昨年末にノンIPA用湿し水「SK-1」を発売しました。「SK-1」はまだ販売期間が3ヶ月にも満たないにもかかわらず、既に10社以上の現場でノンIPA化を実現させています。
弊社の湿し水導入サポートの特長は、印刷経験豊富な技術スタッフがテストに立会い、お客様と一緒に機械の調整をしてノンIPA化を実現するというもので、成功率も高く、お客様には高評価を頂いております。
これを機に皆様の会社でもノンIPA化に向けて真剣に取り組んではいかがでしょうか?
ご用命頂ければ、弊社が全面的にバックアップする事をお約束いたします。 |
|
|
|
|
 |
No.037 |
メンテナンス元年 |
2009/01 |
|
|
明けましておめでとうございます。2007年11月にスタートしたこのコラムも新しい年を迎えることになりました。今年もオフセット業界の皆様の少しでも参考になる情報を発信していけたらと思います。宜しくお願いいたします。
さて、オフセット業界にとっては数々のチャレンジが待ち受けている2009年。 今年のトレンドに目を向けますと、「印刷機のメンテナンス強化」というポイントが見えてきます。
その背景には世界的景気の悪化や銀行の貸し渋りにより、印刷会社がなかなか新台を買えない現状があります。従来の印刷業界は、印刷機を買い替えることにより生産性の向上を実行してきましたが、もはやそれが難しい時代になり、現在保有している印刷機や生産現場の全体を見直して、経費削減や生産性の向上を図ることが必須の1年になると予測されます。
先進的な印刷会社では当たり前のように実行されている点ですが、「うちはまだまだだなー」という会社も多いのでは?
「不況に負けない無駄な贅肉のない筋肉質の現場を作る」
今年はそんな現場作りのお手伝いもして行きたいと、現在準備中です。
詳しくは営業技術部、府中までお問い合わせください。
電話 :06-6334-7300
Eメール : fuchu@sk-liquid.com |
|
|
|
|
 |
No.036 |
時代と共に変化をしよう |
2008/12 |
|
|
2008年も早いもので師走になりました。今年の印刷業界は資材の値上げラッシュと不景気が重なり大変な1年となりましたが、印刷会社の中では儲けが出すぎて仕方がないという会社もあります。全ては時代を先読みしたビジネスプランとその実行努力による結果だと思います。
印刷市場では世界1のアメリカ市場では、インターネットが広まった1995年を境に、印刷会社数の減少が加速し、1995年に6万社あった印刷会社が今日では3万5000社にまで減少しているそうです。
日本でもその流れは起きており、この流れは誰にも止めることができません。従来のビジネスモデルを続けるのみでは成長は難しく、時代に合った新しいビジネスを作り上げることが必須の変革の時となっています。
大変な時期ですが、それだけにやりがいもたっぷり。来年も日本の印刷業界の明るい未来を目指して、盛り上げていきましょう!
当サイトも開始から1年が過ぎました。8月に開始したオペナビも利用して下さる企業様が増えてきて、嬉しい限りです。来年も皆様のお役に立てる情報やプロジェクトを提案していけたらと思います。どうぞ宜しくお願いいたします。
では、印刷業界の皆様、お風邪など召されませぬよう、お体に気をつけて良い年末年始をお過ごし下さい!
|
|
|
|
|
 |
No.035 |
化学物質審査規制法改定について |
2008/11 |
|
|
先月の23日に経済産業、厚生労働、環境の3省合同委員会で、化学物質審査規制法(以下、化審法)を抜本的に改正する法案骨子がまとめられました。次の通常国会に改正案を提出し、2010年度の運用開始を目指す事になったようです。
化審法とは環境への蓄積性が高く、健康被害や環境汚染を引き起こす可能性のある化学物質について製造や輸入等を規制する法律で、1973(昭和48)年に制定されました。「新規化学物質については毒性についての一定の審査を行ない、環境を経由して人の健康を損なうおそれがある化学物質の製造、輸入及び使用を規制する。施行時点で使われていた既存化学物質については国が安全性点検を実施する。」という内容です。もっとも施行後、現在に至っても安全点検はあまり進んでいないのが実状のようですが。
今回の化審法の改定案では化学物質に対する安全基準をREACH(欧州で施行された化学物質規制)などの国際基準にすりあわせることを目的としていて、PRTR制度、GHS「化学物質の分類・表示に関する世界調和システム」の見直し、整合、そして化審法との一体的な改正を指向しているようです。
前回のコラムで指摘しました「各化学物質規制制度のつながりがわかりづらい」が改善され、化学物質の有害性情報が充実していく事は、環境に対応した製品を開発する上で、歓迎すべき事と思います。
しかし、REACH規則に対しては、目的に照らして過剰な義務・負担を事業者に課しており(特に中小企業への負担が過度になりがちです。)、それによって欧州の化学産業の国際的競争力が損なわれる恐れがあるとの指摘もありますので、化審法の改定はその点が考慮されたものとなる事が望まれています。 |
|
|
|
|
 |
No.034 |
枚葉とオフ輪の違い(2)
|
2008/10 |
|
|
『枚葉とオフ輪の違い』第2回目の今回は、紙の違いについて書いてみたい。
枚葉とオフ輪では印刷機の仕様が異なるので、当然、印刷用紙にも違いがあるのだが、別段、材質等に違いがあるわけではない。元々は同一の工程を経て製造された用紙を枚葉用・オフ輪用と分けるのが主で、異なるのは用紙の形態である。
予め用紙の規格サイズにカットされているのが枚葉用紙。平積みで数百部を1梱包にして納品される。一方、オフ輪用紙は『巻取り』とも呼ばれ、カットされていない長い紙がロール状に巻かれている。ロールの中心には芯管と呼ばれる穴が開いており、見たことのない人のために付け加えるならば『巨大なトイレットペーパー』と想像してもらえれば良いだろう。
見た目は異なるものの元を正せば同じ紙。同じ銘柄の用紙で枚葉用・オフ輪用の2種が存在することもある。例えば『SKコート』という印刷用紙があったとすると、材質は同じで形状の全く異なる2種が用意されているわけだ。
(注…中には枚葉専用、オフ輪専用の用紙も存在します。)
以前、用紙を運搬するトラックの運転手さんが『四角い方』『丸い方』などと呼んで用紙を区別していたが、確かに、直接印刷に携わっている人間でないと、両者の違いなど四角いか丸いかの違いでしかないのだろう。しかし、印刷現場で働くオペレーターならば、例え自分の担当機械ではなくても、用紙の違いの意味も知っておいた方がいい。
二者の違いには、印刷機への紙の送り方が異なることが主たる理由にある。
『ツメ』と呼ばれる装置で用紙1枚1枚を挟み込み、印刷ユニットに用紙を送り込むのが枚葉印刷。言わばバトンリレーのようなものだ。一方オフ輪は、紙を送るのではなく引っ張ることで印刷ユニットを通過させる。トイレットペーパーを使用する時、ペーパーの軸を廻すのではなく、先端を引っ張ってカラカラカラッとやるのと同じ。引っ張られた紙が印刷ユニットを通過する際に着肉される仕組みになっている。
二者の違いを見れば、自ずと一つの結論に達する。それが、前号で述べた『印刷スピードの違い』である。用紙を1枚づつ受け渡していくより、一気に引っ張ってあげた方が当然作業を高速化することができる。例えるならば、ティッシュペーパーを1枚1枚取り出すのとトイレットペーパーをカラカラカラッとやるのとでは、後者の方が断然早い、ということなのである。
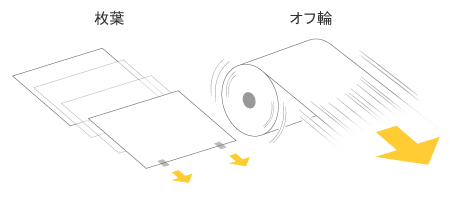
オフ輪の歴史は枚葉より浅い。印刷機の高速化を目指していた設計者が今のオフ輪の基本形を思い付いたのは、ひょっとするとトイレではなかったのだろうか?
などと想像するのも楽しい。 |
|
|
|
|
 |
No.033 |
印材コストの削減について |
2008/10 |
|
|
数年前から多くの印刷現場では、「印材コストの削減」が主要課題となっている。特に今年は原油価格の高騰に伴い印材の値上げが続いているので、これまで以上にコスト意識は高まっているのではないかと思う。自分は印材コストを削減するには、「現場での意識徹底」と「生産性を損なわない印材の選別」の2つが成功の鍵を握ると考えている。今回はこの2点について書きたいと思う。
まずは「現場での意識徹底」だが、自分が訪問する印刷会社でしばしば見かけるのは、資材担当者は高いコスト意識を持っているが、実際に印材を使うオペレーターはコスト意識を持っていないというケース。原因としては現場のオペレーターに印材の価格が知らされておらず、現場では印材は使い放題の状態で、会社の方針がうやむやになってしまっている場合が多い。
例えば、高額な印材であるブランケットの市場での相場は菊半サイズで8,500円、菊全サイズで15,000円前後。大抵、資材担当者は価格交渉を重ねることで14,500円、14,000円といった値引き価格で購入していると思うが、 異物混入のために全ての胴のブランを潰してしまうとすると菊全4色機で約60,000円、8色機で約120,000円の損害が出ることとなる。こういった経験はどこでもあると思うが、果たして現場の全員がその損害の大きさを認識しているだろうか。
「現場での意識徹底」に向けての改善方法としては、現場に印材の価格表を貼りだし、「価格の見える化」を行うことで作業者全員の意識を高める方法がもっとも効果的だと思う。ぜひ参考にして頂きたい。
次に「生産性を損なわない印材の選別」だが、全国の印刷会社を訪問していると、コスト削減のために安い洗浄剤を使い出したが、かえって使用量が増えてしまったり、洗浄力が足りずにカルシウムやストリッピングの発生も増えて以前よりも小まめなメンテナンスが必要となってしまったり等とコスト削減が裏目に出てしまった話をしばしば耳にする。ブランケットにおいても安い製品を使い出したものの、交換頻度が増えたために、年間ベースで考えるとコストが上がり、加えて印刷機の生産性も悪化させてしまったというケースも多々ある。
このように、コスト削減といっても単に単価の安い製品を使えば良いという訳ではなく、「いかに印刷機の生産性を落とすことなくコストが削減できるか」という点としっかりと見極めてから資材変更を行うべきだと思う。
「逆も信なり」という諺もある通り、時にはコストの高い製品を使い続けるという事が正解である場合もある。例えば、当社のロングヒット製品であるABCウォッシュ。この洗浄剤は、強力な洗浄力を持つだけでなく、グレーズの除去、さらにはゴムローラーを長持ちさせる効果も兼ね備えており、使用することにより洗浄時間の短縮と同時に、ローラーに関するトラブルを解消し、結果的には印刷不良の減少と印刷機の高い生産性を可能にするという一石二鳥の製品だ。コストだけを見てしまうとやや高価な洗浄剤ではあるが、コスト以上の効果を発揮するからこそABCウォッシュは長年に渡るヒット商品になっているのだと思う。
このように印材のコスト削減には、目先の価格問題に捉われず、「印刷トラブルを減少できるのか?」「機械のメンテナンス時間を短縮させ、生産時間の向上に繋がるのか?」など、視点を広げて総合評価をする事が大切だと思う。
もし御社が資材コスト削減でお困りの場合は、是非当社にお声を掛けて頂きたい。経験豊富な印刷技術者が御社の担当者と共にコスト削減を実現致します。 |
|
|
|
|
 |
No.032 |
中国ならではの印刷物 |
2008/09 |
|
|
先日、弊社の中国拠点がある大連を訪問し、現地の印刷会社数社で技術サポートを行ってきた。今回はその時に感じたことについて書きたいと思う。
大連の印刷会社で導入されている印刷機はハイデル、ローランドが主流で、リョービや中国メーカーの北人などがそれに続いている。もっとも、北京や上海地区では小森や他の日本メーカーの印刷機も多数存在すると聞いており、状況は殆ど日本と変わらないと思われる。
では、日本の印刷状況と中国の印刷状況では何が違うのだろうか?
自分が一番感じたことは、 所有印刷機の数に対して従業員の数がとても多いということ。ある会社は所有印刷機2台で従業員数300名、別の会社は所有印刷機1台で従業員数200名を抱えていたので、ビックリした。この2社では従業員のほとんどが後工程の部門におり、黙々と手作業で仕事を行っていた。
製品例を挙げると、日本の高級デパートやアパレルブランド向けのペーパーバッグが主で、近年ではこれら高級手提げ袋の6割強が中国で製造され、日本に輸出されているそうだ。
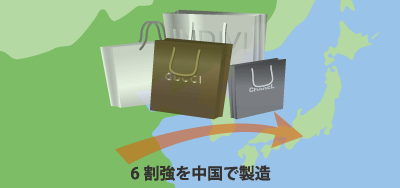
各ブランドが差別化を図るツールの一つとして挙げられているペーパーバッグは、年々より手の込んだ仕様へと変化しており、手作業でしか対応できないレベルに達した物も数多くあるそうで、後工程に人数をかけられる中国ならではの印刷物だなと感じた。品質的にも日本で製造されている手提げ袋と遜色がなく、中国の印刷レベルの向上を感じた訪問であった。
|
|
|
|
|
 |
No.031 |
ロハスな無料求人スペース始めます |
2008/08 |
|
|
今年に入り、原油価格高騰による印刷資材の値上げラッシュで、印刷会社のコストアップは増々大きくなっています。
それに加えて、年々進行する少子化傾向は印刷業界においても例外ではなく、良い人材の確保が難しい「人材難」という問題も出てきているのではないでしょうか。
採用・募集活動におきましては、現在、多くの印刷会社が大手人材会社のサービスを介して行っていると思いますが、その際にかかるコストは、例えば約2週間の掲載で30万円以上もかかってしまうなど、大変高額。コスト削減を第一に考えなければならない状況下で、この投資は決して容易なものではないと思います。
そこで、オフセット印刷.netから新しいご提案です。
この度、当サイトでは、完全無料の求人スペース「オペナビ」を開始することに致しました。
仕組みは簡単。
企業側(印刷会社様)は所定のフォームに募集内容を入力し、当方がそのまま掲示板形式で「オペナビ」スペースにアップ。そして募集内容に興味を持ったオペレーター様が、企業側の指定連絡先に直接コンタクトを取るという流れになります。
当サイトのアクセス数も少しつ づ増えてきておりますので、もしかすると予想以上の効果があるかもしれません。
「印刷業界の資金の流出防止!」
ロハスな印刷業界を目指す当ホームページからのささやかなご提案です。
是非ご活用下さい! |
|
|
|
|
 |
No.030 |
REACH規制について |
2008/08 |
|
|
今回は、欧州連合における環境対策の法律であるREACH, Registration, Evaluation, Authorisation and Restriction of Chemicals (リーチ規制) について説明したいと思います。この法律は EU内部での法制化審議手続を経て、2006年12月にEC規則 として可決され、2007年6月より発効されました。
この規則は既存の化学物質で年間1トン以上使用する製造品・輸入品に対して、その生産者・輸入者が人類・地球環境への影響について調査し、欧州化学庁に登録・公開することを義務づけるものです。情報は原則としてインターネット上で無料公開されます。誰にでも登録できるわけではなくEU内の企業に限定され、域外の業者は域内の業者に登録の代行を依頼するか「Only Representative」と呼ばれる法人に代行させることになります。
対象物質3万種で、登録されない化学物質は域内の製造・輸入・販売を禁止させられることになります。対象物質3万種の内、約1,500 種の物質が「非常に高い懸念のある化学物質」の範疇に入ると推定されています。これらの物質の使用は庁の承認が必要で、この承認については、その物質を安全性がより高い代替物質への切り替えが困難であり、かつ産業活動上使用が不可避な場合にのみ下ることになっています。さらにこの承認を受けるためには、別物質への代替化検討の計画書の提出が求められます。
EU 化学物質政策ディレクターの ナディア・ハヤマ博士は『今日知られている約10万4,000種の化学物質の全ては1981 年以前から製造されているものである。これらは“既存”物質と呼ばれるが、それらが危険なものであるかどうかを調べるためのテストは今までに実施されたことがない。 1981 年以降に市場に出された約4,000 種の“新規”物質に関しては、よりよいデータがある』と指摘していますが、EUに限らず、それは日本においても同じで、製品に使われるいくつもの化学物質のうち有害性が調査、検証されている物質はそれほど多くないのが実情のようです。
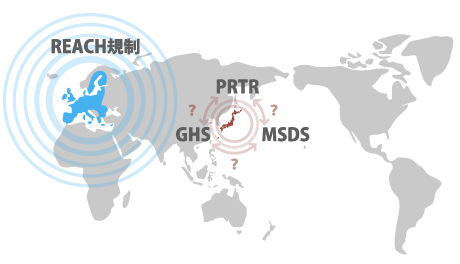 以前のコラムでも指摘しましたが、日本の化学物質規制であるPRTR、MSDS、GHSは肝心の有害性情報が不十分な上、各制度のつながりが解りづらいので、日本でも REACH規制のようなアプローチで既存の化学物質の安全性を早急に明らかにする事、化学物質規制が分かり易くなり、化学物質の有害性情報が容易に入手できるようになる事、より安全な物質の開発と置き換えが推進される事が期待されます。
|
|
|
|
|
 |
No.029 |
枚葉とオフ輪の違い(1) |
2008/08 |
|
|
今回からは枚葉とオフ輪の違いについて書いてみたい。
両部門を併せ持つ印刷会社は数多くあるが、そこで働くオペレーター方は、実は互いの印刷機仕様については、あまり理解していない場合も多いようだ。営業マンとして印刷現場を廻っていて「オフ輪の圧胴ってどこにあるの?」というような見当違いの質問をぶつけてくる枚葉オペレーターも実際に存在する。
自分は、枚葉・オフ輪・フォーム系印刷のオペレーターが集まる飲み会に、年に数回参加する のだが、そこでは「印刷機仕様の違い」「仕事の進め方の違い」などの話題で場が非常に盛り上がったりする。そして「へぇ、オフ輪はそんなやり方するんだ」という風に、意外そうな顔をする者が多いのだ。自分の知り合いに枚葉とオフ輪の両方を経験したオペレーターがいるが「似て非なるもの」というのが率直な感想だそうだ。
印刷の世界も多様化の時代になり、また少人数制でコスト削減を図るのが一般的になりつつある。絞り込まれた少数社員で、数種の印刷機を廻せるスタイルが、これからの時代のニーズになるのは間違いない。そのためには、異なる印刷ジャンルについても今から学んでいく必要があるだろう。
一冊の書籍を考えてみても、表紙は枚葉、本文はオフ輪と別々に印刷することは今や当たり前で、中には見開きページを両者で合わせなくてはならない場合もある。お互いを知ることは、現在の仕事を進める上でもきっと役立つはずである。
数回に渡って両者の違いを書いてみたいが、基本的な話が多く、ベテランの方には退屈な内容になってしまうかもしれない。しかし今回からのコラムは、お互いの違いを知ることに重点を置いているので、その点は容赦してもらいたい。
第1回目としては、先ず、二者の最大の違いについて述べたい。
それは「スピード」である。
当たり前過ぎて申し訳ないが、具体的な数字を挙げたいと思う。
枚葉とオフ輪では用紙サイズが違うため、厳密な比較は出来ないのだが、枚葉機の印刷速度が9000〜12000部/ h程度であるのに対し、 オフ輪は36000〜48000部/hが平均的な数字だ。
単純に考えれば、オフ輪は枚葉の3倍以上の速度で仕事をこなせるのであるから、全ての印刷物がオフ輪へと移行しても良さそうだが、二者には印刷品質の違いというものも存在する。その違いは印刷胴などの機械構造の違いから生じるのであるが、その話は次回以降に。
|
|
|
|
|
 |
No.028 |
ローラー洗浄のポイント |
2008/07 |
|
|
現在の印刷機にはローラーの自動洗浄装置が付いており、ローラー洗浄と並行して別の作業を行なう事が出来るので、作業性を上げる効果的な機能として使用されています。特に最新鋭の印刷機においては、自動洗浄を行う際の回転スピードが大幅にUPしているので、さらなる時間短縮が可能となっています。しかし、ローラー洗浄を自動洗浄のみに頼るのは少々問題があると感じています。
1つ目の問題点は色替え時のローラー洗浄です。大半の印刷機では特色の使用を余儀なくされ、それに伴い色替えが発生します。特に濃い色から淡い色に切り替える場合や、OPニスを使用する際には、前の色がローラーに残りやすく、 それをしっかりと落とす為にローラー洗浄に時間をかける必要がありますが、自動洗浄に使われる灯油もしくは灯油系洗浄剤の洗浄力が足りない為、ローラーの表面に付着したインキを洗い流すことは出来ても、ゴムロール内部に浸透したインキを落とす事が出来ないのが現実です。その為、次の印刷に前の色が出てしまう不良がしばしば発生してしまいます。。
2つ目の問題点は、カルシウムの付着についてです。ここ数年、カルシウム付着によるローラーストリッピング等のトラブルが多発しています。カルシウム付着の一番の原因は印刷用紙である事は確かですが、色替えの場合と同じく、灯油系溶剤にはカルシウム除去効果が無い為、自動洗浄ばかりを頼ったローラー洗浄ではカルシウムがローラーに蓄積してしまい、ローラーストリッピングを発生させてしまうのです。
近年の印刷会社では、材料費のコスト削減に力を入れている事が多く、その中でも消費量の多い洗浄剤はコスト削減のターゲットとなりやすくなっています。しかし、安価な洗浄剤はローラー洗浄の質を下げてしまい、様々な印刷不良の原因を作ってしまいますので、刷り直しが増えたり、機械のメンテナンス時間が増えたりと逆効果もありえますので資材の選定には注意が必要です。
その反対に、洗浄力の高い洗浄剤を使用すると、一見コストは上がったように見えますが、実は少ない使用量でローラーに浸透したインキを落とす事が可能になりますので、使用量の削減と洗浄時間の短縮、さらに、カルシウム除去効果も含まれていれば、専用のカルシウム除去剤の使用量を減らす事ができ、ローラーストリッピングの防止、そして最終的にはローラーの交換周期や印刷機の生産性にも好影響を及ぼします。
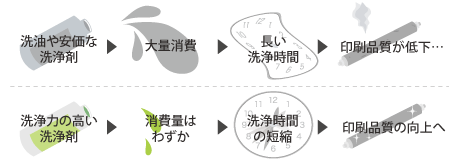
弊社では、ローラー洗浄に関わるトラブルやコスト削減のお悩みについて解決する為に、洗浄剤の選定から実際の印刷機を使っての洗浄デモンストレーションを行っております。現在のローラー洗浄方法がベストではないなとお感じの場合は、お気軽に弊社営業技術部までお問い合わせ下さい。電話:03-3856-5111 |
|
|
|
|
 |
No.027 |
今、何故UV印刷なのか? |
2008/07 |
|
|
従来UV印刷と言うと特殊印刷やパッケージ印刷が主流でしたが、近年は一般商業印刷分野でUV印刷機を導入するケースが非常に増えています。では、何故よりコストの掛かるUV印刷が増えているのでしょうか?
一部で景気回復の兆しが有ると言われている中、我々の印刷業界は以前に増して厳しい状況が続いています。用紙の値上げ、原油価格の高騰による諸材料の値上げなどで製品原価が上がる一方、印刷各社の低価格競争が激しく、原価高を販売単価に反映出来ないのがその背景にあります。それでもコストの高いUV印刷機を導入するのにはそれなりの理由が挙げられます。
- 用紙以外の特殊原反への印刷が可能。
- 後加工が直ぐに行える。
- デリバリーでの棒積みが可能。
- 乾燥待ちのスペースを削減。
- スプレーパウダーが不要。
- 耐摩擦性に優れている。
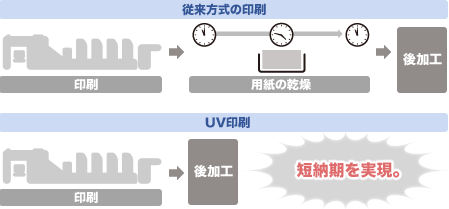
UV印刷により、高付加価値印刷や短納期を実現させ、これらを武器に受注量を増やす。また、作業改善を図り、稼働率のアップと不良率を軽減させて無駄な経費を削減する。この差別化と作業改善で現在の厳しい状況を打破しようとしている印刷会社の意図が伺えます。
他社と同じ方法で同じ仕事をしていては、価格競争を招くことになり、またその競争からも脱落していく危険性があります。近年のUV印刷の増加は上記のメリットを最大限に活かし、他社との差別化を図る事が生き残りの手段と捉えている会社が増えているのが背景にあるのだと思います。
しかし、メリットもあるUV印刷ですが、当然デメリットもあります。この点についてはこれからのコラムで触れられたらと思います。 |
|
|
|
|
 |
No.026 |
ドルッパと印刷業界のグローバル化について |
2008/06 |
|
|
ドルッパ出張の為、コラムの更新が遅れてしまいました。どうも済みませんでした。
4年に1度の印刷の祭典であるドルッパに行ってきました。4日間の通し券がなんと3万円もする!としょっぱなから驚かされましたが、17ホールもある展示会場をランニングシューズ(絶対にお勧め)で歩き回り、最新の印刷事情を吸収して来ました。
ドルッパ中は各国の印刷関係者がデュッセルドルフに集まり、街は一種のお祭り騒ぎになります。ドルッパはデュッセルドルフの街を上げてのイベントなので、バス停等のいたる所に、「ようこそドルッパへ」といった広告が張ってあります。展示会の後は、関係者が一同、旧市街に集まり、ビールを酌み交わしながら、騒いでいるのもドルッパ名物となっています。
当社の一行も、毎晩海外取引先との夕食の連続で、華やかなドルッパの雰囲気を満喫して来ました。
そんなある日の事ですが、イギリスの取引先と夕食をした所、スロベニアの資材会社、ポーランドのローラー会社、リトアニアのハイデルベルグの営業さんも参加する事になり、ちょっとした印刷ワールドカップが始まりました。ポーランドの印刷技術者と湿し水の導入方法を議論したりして、当社の技術も楽しんでいました。当社は海外の多くの国々と取引をしていますが、今まではいわばアメリカ、イギリス、イタリア、ドイツ、フランスといった先進諸国が主で、東欧の国々は初めて。しかし、印刷業界のグローバル化が進むこれからは、このような国々の人達とも取引をしたり、競合をしたりするんだろーなーなどと考えつつ夕食をしました。
今年になり業界縮小のスピードが進んでいる日本のオフセット業界。これからの時代は市場を日本だけではなく、お隣の中国やアジア全体に向けなければと当社も現在中国で活動中です。
そんな時に支えとなるのが、日本人の良さである勤勉さ、ディテールにこだわる繊細さ、そして「お客様は神様です」というフレーズに象徴される日本特有のおもてなしの心。これらを武器に世界からの競合と闘っていく時代が来ていると感じた今回のドルッパでした。
|
|
|
|
|
 |
No.025 |
MSDS・GHSについて |
2008/05 |
|
|
今回は基本的な化学物質管理制度の一つである『MSDS』、『GHS』について説明したいと思います。
「MSDS制度」とは、対象化学物質が含まれる製品を他の事業者に提供する際に、「製品安全データシート:Material Safety Data Sheet 」と呼ばれる、化学物質の性質、危険性、取り扱いに関する情報を事前に提供することにより、化学物質の適切な安全管理に役立てることを義務づける制度で、法律、政令で指定されるMSDS提供義務のある化学物質は約1500物質あります。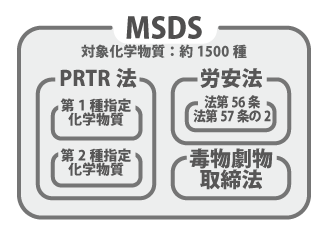
「MSDS制度」も2008/2/4(No.010)のコラムで説明した「PRTR制度」も化管法(特定化学物質の環境への排出量の把握等及び管理の改善の促進に関する法律)に基づいて導入された制度で、両制度の実施により事業者による化学物質の自主的な削減努力を促し、環境の保全上の支障を未然に防止することを目的としています。(※ユーザー事業者は提供されたMSDSの情報からしか、PRTR届出の必要を判断できません。)
MSDSは国際物流においても重要ですが、これまで各国でその内容などが異なっていたため、これを統一したものにしようと国連が各国に勧告・公表したのが「GHS」です。GHSとはグローバル・ハーモナイズ・システム(化学品の分類及び表示に関する世界調和システム)の略になります。化学品の危険有害性に関する情報を正確に伝え、安全と健康を確保し、環境を守るという目的で、化学製品に関する危険度が一目でわかるよう、世界的に統一した基準で分類して製品に絵(シンボルマーク)で表示する制度です。 平成18年12月1日には日本でも導入が実施されました。MSDSにシンボルマークで表示・提供義務のある物質は約640物質、内99物質は製品容器ラベルにシンボルマークで表示する義務がある物質です。しかし、この数字は「すべての有害物質を対象にする」というGHSの本来の趣旨から考えると、少ないと感じられるのも否めません。
また、MSDS、GHSいずれの制度も、化学製品が製造・輸入業者→中間業者(加工、卸売、小売)→消費者という過程で、情報を消費者に伝えるまでは義務づけられていないので、(*中間業者=消費者の場合は除きます。)消費者は自ら情報を集めなくてはいけません。その場合、内容も専門的な上、各制度の関連が複雑で理解できないのが実情です。
『消費者に化学品の危険有害性に関する情報を正確に伝え、安全と健康を確保する』という化学物質管理制度の基本的な目的実現の手段になるように、今後、包括的でわかりやすい内容に制度改正されることが望まれます。
弊社でも、お客様(中間業者=消費者)に製品を紹介させて頂く際に、製品のラベル表示、技術資料・カタログ・MSDSなどから危険有害性情報を提供させて頂いていますが、これからも内容面で、よりわかりやすい表記を心がけたいと思います。 |
|
|
|
|
 |
No.024 |
飲み会のススメ |
2008/05 |
|
|
さまざまな印刷会社を訪問して現場を見ていると、早番・遅番・他チームとの意思疎通ができていなかったり、後輩へきちんと仕事を教えていない会社が割とあると感じることがある。
この傾向は、オフ輪工場で特に感じるのだが、その理由は以下の2つが根底にあるのではないかと自分なりに考えている。
(1)工場が都市部・駅から離れた地域(工業団地等)にある
(2)交代制を実施している
(1)は環境問題等の関係上、むやみに住宅地近辺に建設できない事情からなる。また、オフ輪工場は広い敷地を必要とするので、家賃の都合もあり、近年は郊外に工場を構えるのが普通になっている。
(2)は以前のコラムにも書いたが、印刷単価の下落・短納期に対応するため、印刷機をフル稼働させる必要が生じたからである。現在のオフ輪会社は、2〜3チームの交代制(24時間制)を敷くのが主流となっている。
これがなぜ、意思疎通の欠乏につながるのか? 理由は1つ。
『飲みに行けないからである。』
あえて酒の席にする必要はないかもしれないが、職場から離れた場所で飲んだり食べたりしながら、普段は交流する機会の少ない他チームのメンバーとゆっくり話をすることは、非常に有意義であると思う。勿論、職場ではノートなどに申し送りを記入し、必要事項を伝達しているとは思うが、食事でもしながらゆっくりと話をすれば、普段言いにくいことや細かなことまで伝えられるはずだ。
また、若手オペレーターは、先輩に仕事を教わる大チャンスでもある。印刷現場というのは非常に慌ただしい場所なので、作業をしながら親切丁寧に細かいところまで教えるというのは、実際問題としては難しい。飲み会の席は、若手オペレーターが、日頃疑問に思っていることを先輩から聞き出すのに、絶好の場となる。
自分のオペレーター時代初期は、幸運にも会社が駅から近いところにあり、さらに24時間制も行なっていなかったので、印刷部全体での飲み会がよく開催されていた。その席で日頃の疑問を先輩オペレーターにぶつけ、また、他チームのメンバーと仕事の進め方などの意見交換ができた。今思えば、現場で汗水流すのと同じくらい貴重な時間だったと感じている。
(1)や(2)の体制ができあがってしまっている印刷会社では、全オペレーターが出揃うような飲み会の開催は非常に難しいことである。さらに、営業部員と連携するために、印刷機を停め、時間を作る必要もあるだろう。しかし、このような飲みニケーションが機能すれば、現場の連携がアップし、若手の技術が向上し、ベクトルが一致し、結果として部員が一丸となって印刷品質を追求するような現場発の相乗効果が生まれると思う。
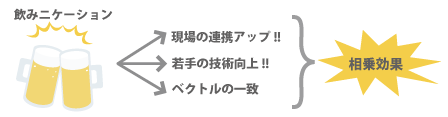
あなたの会社でも、年に数回、印刷部全体での飲み会を開催してみてはいかがだろうか? |
|
|
|
|
 |
No.023 |
ブラン下の胴仕立てについて |
2008/05 |
|
|
ブラン下の胴仕立ては安定した印刷品質を求めるうえで非常に重要な役割を担っている。その標準的な仕立て方法は、ブランとブラン胴のベアラーを同じ高さに仕立てるものだが、ブランや下紙のヘタリを考慮して0.05mm高く仕立てる 「オーバーパッキング」が現在の主流となっている。仮にそれ以上高く仕立ててしまうと、網点太りやダブり、さらにローラー目が出やすくなる等のトラブルを招くので絶対にNGとなる。逆にベアラーに対して低くなればなるほど、網点やベタの着肉不良に繋がるのでこれもNG。胴仕立ての100分の1mm単位のわずかな違いが、印刷の再現に影響を与えるのである。
しかし、この重要な胴仕立ては、湿し水の管理やローラー調整等と比較して、軽視されがちな存在である。
その理由の一つとして、シリンダーゲージを用いた計測方法にあると自分は見ている。シリンダーゲージでの仕立ては、ブランとベアラーとの高さの差を計測して割り出すものだが、シリンダーゲージは曲面のブラン胴に密着させるので、少しでも手元が狂えば大きな数値の変化を招いてしまう。計測は100分の1mm単位で行なう為、何度測っても数値が安定せずに最終的には計測を諦めてしまうパターンが多く、その結果として仕立ての計測そのものを怠ってしまう傾向が強いと自分は考えている。実際に、営業訪問や技術訪問の際に客先で仕立て管理についてよく質問するが、管理意識をしっかり持っている会社は数えられる程少ない。大半の印刷会社は、上記のような理由で仕立て管理から遠のいているのだと推測する。
この問題を解決する為に、当社で扱っている『デジ・ブランケット』というパッキングゲージを紹介したい。この製品は、仕立てをブランとベアラーの高さの差で計測するのでは無く、仕立てそのものをデジタルの実測値で表示する特徴を持つ。例えば、ブラン1.95mm+下紙0.9mmで仕立てた場合、2枚の合計となる2.85mmと表示される。 デジ・ブランケットを使うとセンサーをブランケットに当てるだけで、「2.85mm」と表示されるので、測定がとても簡単。そして、ブランケットを使い込んでいくうちに数字が減少してくるので、ヘタリ具合も一目瞭然となる。最近では、ベアラー部分が隠れてしまっている印刷機も多くあるので、このような機械では特にユーザーでも喜んで使用して頂いている製品だ。
計測についての問題を解決したら、後はどこまでのヘタリを自社の許容範囲とするかを決定してしまえば仕立て管理は完璧。許容範囲は印刷機や使用しているブランによって変わると思うが、新品の状態からマイナス0.07mm辺りがラインとなる。これを超えてしまった場合は、胴張り用紙の追加やブランケットの交換を行ない、規定の高さまで戻すことで着肉不良などのトラブルを防ぐことが出来る。
より安定した印刷物を作り出す為には、仕立て管理についても、是非一度再検討して頂きたい。特にCMSを実行もしくは検討している場合には、しっかりとした管理を行ない、常に同じ胴仕立ての状態で印刷を行なえるようにするべきだと思う。 |
|
|
|
|
 |
No.022 |
drupa(ドルッパ)2008に向けて |
2008/04 |
|
|
印刷業界に携わっている人であれば、「drupa(ドルッパ)」という展示会はご存知でしょう。
「drupa」は、世界1の規模を誇る印刷関連の総合展示会で、4年に1度ドイツのデュッセルドルフで開催されています。 印刷業界には、「PRINT(アメリカ)」、「IPEX(イギリス)」、「IGAS(日本)」、そして「drupa(ドイツ)」という世界4大展示会があり、「drupa」はその中でも最大規模。毎回オリンピックイヤーに開催される事から、「印刷界のオリンピック」とも呼ばれており、今後の印刷界の鍵となる新技術が発表される場として、世界中から注目されています。
drupaの歴史ですが、今から57年前の1951年に、当時のハイデルベルグ社のシュテルンベルグ社長の提唱の元、第1回目が開催されたそうです。ちなみに、この「ドルッパ」という言葉ですが、ドイツ語のドルック(印刷)と、パピル(紙)を合わせた造語とのことです。
今年は第14回目となるdrupaの年で、5月29日から2週間にわたり「drupa2008」が開催されます。発表資料によると、会場面積は、前回の16万uから17万uに拡大、参加企業は18,000社を予定し、50年の歴史の中で最大規模のイベントになるそうです。
過去3回のdrupaを見ると、95年は「CTP drupa」、2000年は「デジタル drupa」、2004年は「JDF drupa」と呼ばれました。今回は「インクジェットdrupa」になると予想されており、各社の新機種の完成度が注目されています。
私は、印刷業界に20年以上携わっていますが、このドルッパで発表される新技術にいつも驚かされています。今回は、どのような新技術に巡り合えるのか、今から非常に楽しみにしています!
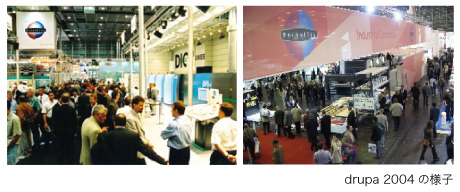
|
|
|
|
|
 |
No.021 |
そろそろ植物油でしょう |
2008/04 |
|
|
原油価格の値上がりが止まらない。Yahooで「輸入原油価格」と検索してトップに出てくる垣見油化のデータによると、今年2008年2月の原油価格は1バレル(159L)92.7ドル。昨年の2007年の2月は55.08ドルなので、 この1年間でなんと68.5%も上昇している。
石油ベースの材料を大量に使用する印刷業界は必然としてこの上昇の波に巻き込まれている。馴染みのインキメーカーの人間と最近話したが、昨年やっとの思いで値上げを敢行したが、その後も原油価格は上がる一方で、実際は再度値上げが必要で、他社の出方を伺っている状況とのことだ。
そんな中、今回のコラムで紹介したいのが、植物油ベースの洗浄剤「エコウオッシュ」。当社が1996年より販売しているスイス製の洗浄剤で、すでに12年の実績を持ち、全国の印刷会社で使用して頂いている。
石油系洗浄剤とは違い、植物油ベースの洗浄剤なので、オペレーターの健康にもやさしく、工場内の臭いも抑え、万一下水に流れてしまっても微生物分解性を持つので安心という、文字通りエコな洗浄剤だ。
この製品は絵画の画家さん達にも人気で、全国の印刷会社に交じって、個人の画家さん達からも注文が入るユニークな存在。臭いのきつい石油系のクリーナーと違い、明らかに体に良いと実感ができる、との評価を頂いている。
なにせ、一番の魅力は原材料が植物であるということ。これから枯渇していく石油と違い、資源に限りがないため、値上げの心配が一切なし。実際現在の価格は12年前の発売当初と全く同じである。
石油製品を使い、これから毎年のように舞い込む値上げのお知らせに激怒し続けるよりも、いっそ植物油の洗浄剤に移行して、心にも体にもやさしく印刷をするのはいかがだろう?
そろそろ植物油でしょう! |
|
|
|
|
 |
No.020 |
PFOAとPFOSについて |
2008/04 |
|
|
最近、弊社製品にPFOA(パーフルオロオクタン酸)または、PFOS(パーフルオロオクタンスルホン酸)が原料として使用されていないかとの照会を多く頂いてますので、この場をお借りして、PFOA、PFOSとはそもそもどのような物質かについて説明したいと思います。
この2種類の物質は、化学構造的に直鎖状に並んだ8個の炭素原子すべてにフッ素原子が結合しており、末端にスルホン酸基(PFOS)やカルボン酸基(PFOA)が結合した構造を有することから、水だけではなく、油や有機溶媒も弾くという特殊な性質があります. その利便性から、類似化合物を含めて日用品にも多く使われており、その用途は界面活性剤(洗浄剤)、消化剤、焦げ付かないフライパン(商品名:テフロン、シルバーストーン)、紙のコーティング、防水スプレー(商品名:スコッチガード)、車のワックス,撥水加工のレインコート(ゴアテックス)、防汚剤等として幅広く使用されています。
このPFOAとPFOSという物質は、半世紀以上使用されてきたにも関わらず、近年、人間、動物に対する高リスク(発がん性、免疫系障害、生殖障害、先天性障害)が確認されており、世界的に使用規制がかかっています。
PFOAとPFOSの最も大きな問題は、環境中で分解する能力が全く無く、生物蓄積性をもつ事です。他の残留性有機汚染物質ですと、少しは環境中で分解して行きますが、この2つの物質は、たとえ製造が禁止されても、過去に製造された分が永久に自然界に残留し、環境、食物連鎖を通じて、再び拡散し続けるであろう言われています。事実、現在では製造メーカーが生産を中止したり、全体の生産量は大幅に減少していますが、この2つの物質は環境中から検出され続けています。
環境中で検出されているPFOAとPFOSの源と経路が現段階では科学的に解明することが出来ない為、これらの物質は完全に使用禁止とはなっていませんが、各国で削減を促す規制が増えています。
EUではPFOS規制があり、EU内へ運び込まれる産業製品の指定含有量が最大0.005%と決まっています。北欧のストックホルム条約では残留性有機汚染物質(POPs)としてPFOSが追加提案されています。アメリカではEPA(米国環境保護局)が特定の州で飲料水源中のPFOA許容濃度を定める方向で動いています。日本では、第二種監視化学物質(化審法)に指定されています。
印刷関係では写真平版プロセスや産業的写真コーティングなどで使用されているようですが、弊社製品郡(洗浄剤、湿し水等)でPFOA、PFOSを含有している製品はありませんし、弊社の方針として、今後の製品開発でもPFOA およびその他の化学物質で環境中や人間の体内でPFOA に分解する可能性がある原料は、使用しないようにして行きたいと考えております。 |
|
|
|
|
 |
No.019 |
目指せ90点 |
2008/04 |
|
|
印刷現場で約10年間働いて思い知ったことがある。
それは「印刷で100点満点は不可能」ということ。
のっけからネガティブな発言で申し訳ないが、少し我慢して読み進めていただきたい。
印刷現場では見本紙を参考にして色を合わせていく。今さら説明するまでもないことだが、見本紙とは色調、誤字・脱字の有無などを予めお客様に確認してもらい、OKをいただいた印刷物である。
ところが、見本を刷った印刷機と本印刷の印刷機は異なることが多い。印刷機の機種が違うと、同じように色を表現することが難しいのだ。
また、くわえ側・くわえ尻側でうまく色を調整出来ないこともある。くわえ側は赤くしたいが、くわえ尻側は赤味を抑えたいなんていうのはよくある話。片側を見本に合わせれば、もう一方は当然、見本紙と異なってしまう。
見当も同様のことが言え、駆動側(G側)が合っても操作側(M側)がズレてしまうことなどは多々ある。
このような場合、
- 2者の中間に合わせる
- 重要な面(表紙・広告面など)を中心に合わせる
などの措置を取る。
見本と全く同じは不可能だとしても、どれだけ見本紙に近づけることが出来るかが、オペレーターの腕の見せ所となるのだ。
もし見本と寸分違わぬ100点満点を目指すとしたら、印刷の度に版をデータから作成し直したりインキを変更したりと、そこには膨大な時間と費用が掛かってしまう。そして、例えそれを実行したとしても、見本と全く同じようには印刷出来ないだろう。自分は10年間のオペレーター生活で「今日は完璧だ」と思えたことは1度たりともなかった。
そこで発想の転換だ。
100点を目指すのではなく「いかに減点材料を減らすか」と考えるようにしたらどうだろう。 ネガティブ要素をポジティブに変換するのだ。 「完璧にやれ」と言われると、人はウンザリしたりプレッシャーで潰されそうになったりするが、「なるべくマイナス要素を減らせ」なら実現可能で目指しやすい。目指すべくは90点台なのである。
マイナス材料を減らす土台には、印刷機や印刷現場の環境を、常に一定の高水準に保つということが挙げられる。
例えば
- 日常的なグレーズ・カルシウム処理、ローラー調整でローラー状態を安定させる。
- 温湿度計など使用しながら空調・加湿を管理し、インキ・紙の品質を保つ。
- 湿し水を安定させるために、H液を定量装置で管理する、循環機を定期的に清掃する、水温のチェック・調整をマメに行なう。
などなど。90 点を目指す上で、取り敢えずは70点は確実に取れるような用意をしておきたい。この70点分が今述べた日頃のメンテナンス・環境管理なのである。印刷材料メーカーは、この70点をコンスタントに取るお手伝いの為に存在していると言ってもいい。だからこそ自分達が印刷現場を訪問した時には、要望や質問の声をどんどんぶつけて欲しい。
そして、残りの20点は…
それはオペレーターさんの腕に掛かっているのです! |
|
|
|
|
 |
No.018 |
ローラー交換サービスを通して |
2008/03 |
|
|
昨年から当社ではローラー交換サービスを開始している。私は印刷オペレーター出身なので、普段の営業活動に加えて、ローラー交換サービスのメンバーとしても活動をしている。印刷機のゴムローラーの交換目安は、インキング部で1年、給水部では半年となっている。定期的な交換を行わないと、インキや湿し水が正しくローラーを伝わらない為に、インキの転移不良や汚れ、ゴミの付着等の問題が発生する。しかし、交換には時間がかかり、1ユニットの交換で最低2時間を費やすのが実状。更に、ユニット内部の清掃等を含めると実際には3〜4時間かかってしまい、印刷機が4色機ならば1日、8色機ならば2日機械を止めて作業を行うこととなる。言うまでもなく、印刷会社が1日機械を止めることは大きな生産ロスに繋がる。そこで、週末などお客様の空き時間を利用してローラー交換作業を代行するのが、当社のローラー交換サービスである。
作業の流れとしては、ローラーを外す→金ローラー磨く→ユニット内部の清掃→ローラー組み込み→ニップ調整→印刷立会いという流れで進行し、所要時間は2人作業で1ユニット4時間前後となる。ポイントとなるのは金ローラー磨きの部分で、金ローラーに蓄積したグレーズやカルシウム成分を、当社のグレーズリムーバーで念入りに磨き、金ローラーも新品同様に仕上げてから組み込んでいる。 それにより、ローラーストリッピング等のトラブルが大幅に軽減されるとお客様から好評を得ている。
また、ニップ調整ではデジニップを使い調整を行っている。デジニップを使用することでニップ調整の時間が従来の半分以下に抑えられ、なおかつ正確で的確な調整が出来るので、作業をする側も楽だし、お客様にとっても時間でチャージされる作業費が低くなるので喜ばれている。
ローラー交換の仕事は印刷機の止まる週末に入ることが多いので、休日出勤を余儀なくされてしまう。しかし、ローラー交換での訪問は、普段の営業訪問の「お客様対営業」といった関係ではなく、同じ印刷人としてオペレーターさん達と1日を過ごせるので、私にとっては貴重で有意義な時間となっている。
当社は印刷現場に関わる製品を幅広く扱っており、ローラー交換メンバーも全員オペレーター出身な為、ローラー交換をしながら、お客様から様々な日頃の問題点を質問され、その一つ一つに対応している。今後もローラー交換サービスを通じて、お客様の印刷に関しての日頃の問題点を解決する総合的なサポート役を目指して日々の勉強をしていきたいと思う。 |
|
|
|
|
 |
No.017 |
メンテナンスと生産性 |
2008/03 |
|
|
近年、小ロットや短納期が当たり前の世の中になり、印刷現場では、毎日納期に追われて、目の前の予定を消化する事に集中しているのが現状だと思います。確かに、現場としては印刷機をどれだけ稼動するかが生産性を向上させ、会社の売上と利益に繋がります。しかし、印刷機の稼働率ばかりを追求することは本当に会社のメリットとなるのでしょうか?人間も時には体を休めたり、ケアするのが必要なのと同じく、印刷機も定期的なメンテナンスが必要です。このような事を言うと、「既に自社では定期メンテナンスを実施しているし、メンテナンスの重要性も理解している」との反論も有るかと思いますが、私自身が毎週のように全国の印刷会社を訪問して感じるのは、メンテナンスの重要性を理解して、定期メンテナンスを実施している会社は意外に少ないものだという事。そのような背景があり、今回はもっと印刷機を愛してほしいとの願いを込めてコラムを書いています。
印刷現場として生産性を上げる事も大切ですが、印刷の刷り直しや機械の修繕費といった余計な出費を出さない事も非常に大切な事です。年間の修繕費の内訳を調べると、中にはもちろん突発的な故障も有ると思いますが、経験上、未然に防げるトラブルが半数近くに上るのではと思います。例えば定期的に給油またはグリスアップを怠った事によるマシントラブルなどは、調査すると数多く有るものです。
現場の責任者や経営者の立場から考えると、勤務時間内に機械を止めてメンテナンスを行う事に強い抵抗を感じるかもしれませんが、印刷トラブルを未然に防ぐためにも、是非定期メンテナンスを仕事の一環として捉えてほしいと思います。 そしてオペレーターの皆さんには、もっと印刷機を大切にしてほしいと訴えたい。例えば、自分の愛車に関しては定期的にオイル交換や洗車もする。これは自分で苦労して手に入れたという意識を持っているからこその行動だと思います。それと同じように、印刷機は会社から与えられた物ですが、自分の給料を生み出してくれる大切なツールです。そういった意識を持って印刷機と接するようになれば、自然とメンテナンスをやろうという気も起り、その結果「印刷トラブルの減少」、「印刷品質の向上」、そして「生産性の向上」という、会社にも自分にもプラスになる相乗効果に結びつくと思うのです。
印刷機の定期メンテナンス。まずは一つずつ、丁寧に。是非実行してみて下さい。 |
|
|
|
|
 |
No.016 |
コーヒーブレイク |
2008/03 |
|
|
このコラムを担当するのも4回目となり、メンバー達もネタ探しに苦労をし始めているようです。そんな自分もその1人。今回は印刷の話から離れ、ちょっとコーヒーブレイクという事で、スターバックスコーヒーの話をしようと思います。
自分はスターバックスコーヒーの大ファンです。日頃街でスタバの店を発見すると、凄く嬉しくなるし、平日仕事をしつつ、スタバで打ち合わせが出来る日などはとても幸せになります。
スターバックスは単にコーヒーが美味しいというだけではなく、お洒落なインテリア空間、教育が行き届いた従業員、続々と出てくるCDやマグカップ等の関連グッズがいつも心地よい気持ちにさせてくれるし、従来1杯150円程だったテイクアウトコーヒー市場に対して、倍以上の1杯350円でもお客様を呼び込むブランドを確立した会社としても尊敬の念を抱いています。
そんな自分が、先週はバンクーバーに出張。ホテルに到着してテレビをつけると、スタバについての素晴らしいニュースが飛び込んできたので、この場を借りて皆さんに紹介しようと思います。
アメリカ・ワシントン州のタコマという街のスタバに毎朝通うアナマリー・オースネスさん(55歳・女性)は腎疾患を20年程前から患っており、最近主治医から肝臓機能がひどく低下し移植が必要と宣告されました。通常は家族の中で移植に適合するタイプが居るものですが、彼女の場合は運悪く誰も適合せず、一般から臓器提供者を探すことになりました。しかし、適合する肝臓を持つドナーを探し出すのは至難の業。アナマリーさんはとても落ち込んでしまったそうです。
そんなある日、毎朝アナマリーさんのコーヒーを作っているスタバの女性従業員のアンダーソンさんが、元気のないアナマリーさんに気付き、事情を聞いた後に驚くべき事を言いました。なんとアナマリーさんの為に、自分の肝臓が適合するかテストに行ってみるわ、と答えたそうです。
そして数日後、いつものようにアナマリーさんが朝のコーヒーを頼むと、アンダーソンさんがとびきりの笑顔で、「適合したわよ!」と伝えたそうです。2人はその場で手を取り合ってワンワンと泣き出したそうです。
そしてその手術が先週の3月11日にシアトルの病院で行われ、アンダーソンさんの右の肝臓がアナマリーさんに無事に移植成功。このニュースは「スタバの従業員がメニューにない素晴らしいプレゼントをお客様に提供!」として全米でニュースとなりました。
明るいニュースが少ない印刷業界ですが、こんな元気が出るニュースも良いものですね!
ニューヨークタイムズ ウェブ版
http://www.nytimes.com/2008/03/04/us/04barista.htm |
|
|
|
|
 |
No.015 |
石油系溶剤(洗浄剤)の危険性、取り扱いについて |
2008/03 |
|
|
今回は、洗浄剤の主成分である石油系溶剤の危険性について説明したいと思います。
石油系溶剤は、主にガソリン、灯油、軽油に相当するものを化学処理して製造されます。
種類によって物性はかなり異なりますが、中でも共通する特性としては揮発性(蒸発して気体になる性質)、可燃性、脂溶性(脂質を溶解する性質)の三つが挙げられます。
一般的に有機溶剤の危険性としては『火災』と『中毒、皮膚刺激』があり、『火災』は揮発性と可燃性に、『中毒、皮膚刺激』は揮発性と脂溶性に関係があります。
先ず『火災』についてですが、可燃性液体から発生する蒸気が着火源にふれて炎上する現象を引火といい、蒸気が引火を起こす濃度に達したときの液体の温度を引火点といいます。
引火点が30℃未満のものを引火性物質、30℃以上100℃未満のものを可燃性物質といい、火災危険性の高いものは消防法により危険物と指定され、貯蔵や取り扱いについて様々な規制が設けられています。引火性液体は消防法で第4類に該当し、更に引火点が21℃未満のものは第1石油類、21℃以上70℃未満のものは第2石油類、70℃以上200℃未満のものは第3石油類と分類されます。
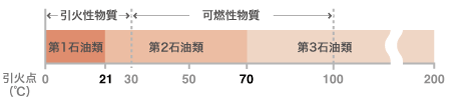
但し、溶剤が紙や布にしみこんだ場合は引火点より低い温度で着火する場合もある為、より一層の注意が必要になってきます。
次に『中毒、皮膚刺激』についてですが、溶剤が皮膚や粘膜に付着した場合、その脂溶性の為に刺激作用を起こし、そういった付着が繰り返されることで皮膚の脂肪が失われて炎症、ひび、あかぎれを起こす他、皮脂線を通して体内に侵入していきます。また、その揮発性の為に、蒸気となって呼吸の際に肺から人体へ吸収され、許容量を超えると中毒症状を起こす場合があります。体内に吸収された溶剤による中毒としては、急性と慢性の病状があります。急性中毒は高濃度の蒸気を吸入した場合に起こり、一時的に脳や神経の機能が失われて麻酔状態が現れます。そして極めて濃度が高い場合には意識不明、死亡する事もあります。慢性中毒は低濃度の蒸気を長期間吸入した場合に、神経障害、頭痛、めまい、肝障害などを起こす様を示します。
石油系溶剤の中毒危険性に関する法令の一つとして有機溶剤中毒予防規則(有機則)があります。有機溶剤を製造、または取り扱う際の健康障害を予防することを目的としており、溶剤中毒の危険性のある54種類の有機溶剤が指定されています。有害性の程度のより大きいものから、第1種〜第3種に区分されており(※石油系溶剤で第1種に指定されているものはありません。)、有機則の規定は要点を挙げると以下の通りになります。
- 衛生管理体制‥規定している溶剤を取り扱う場合、事業規模により衛生委員会(統括安全衛生管理者 他)を設ける。
- 環境管理‥第1種〜第3種に応じて、排気設備、換気設備を設ける。
- 作業管理‥作業場に、溶剤の人体に及ぼす作用、注意事項、応急処置を掲示する。作業環境濃度の測定を義務付ける。
- 健康管理‥保護具の着用、定期的な健康診断を義務付ける。
作業環境を安全な状態に保つには、扱う洗浄剤(他化学製品)の危険性を十分に理解して、細かいことと思うことでも法令などの規定をきちんと守って作業するのが最も大切であると思います。弊社におきましても、引き続き製品に含まれる化学物質とその安全情報を提供していく事に努めていきたいと思います。 |
|
|
|
|
 |
No.014 |
テンション調整 |
2008/03 |
|
|
オフ輪印刷で重要なポイントは?というようなことを聞かれた時、自分は「テンション」と答えることにしている。
勿論、「湿し水」「ローラー状態」「ブランケット」など他にも大切な要素はある。あるが、そんな中でも自分は先ず「テンション」を挙げる。
湿し水やブランケットを指摘する材料メーカーは多いが、テンションに言及する人間はあまりいない印象がある。
湿し水の不具合と言えば、汚れなど絵柄上のトラブルだけであるが、テンション調整がきちんとなされていないと、見当や折り精度、シワの発生など様々なことに悪影響を及ぼす。人間の身体で言えば肝心要の「腰」の部分に該当すると言えるかもしれない。
テンションは、「インフィード(給紙部からドライヤー出口まで)」「クーリング」「ウェブ(折り機)」の3ヶ所のバランスで調整される。具体的な設定値は、機種や紙の斤量などにより異なるのでここでは説明出来ないが、とにかく3者のバランスが重要である。
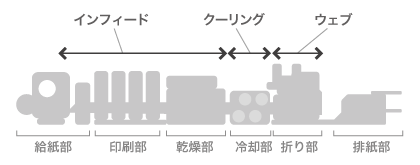
インフィードが強過ぎるとシワが発生したり、ウェブが弱いと折りズレが生じたりする。適切な設定は経験で得ていくしかないが、経験の少ない若手オペレーターは、テンションを重要視しない傾向があるように思われる。少なくとも水やブランケットを気にする程には、注意を注いでいないだろう。
ベテランオペレーターには「当たり前だろ」と叱られてしまいそうだが、もしこのコラムを若手のオペレーターが読んでいたら、今後は少しテンションを気にしてもらいたい。走行中の紙が適切なテンションでピンと張られていると、見当や折り精度がとても安定する。特に一昔前のオフ輪機はテンション調整が全て手動であるので、色々と操作してみて、紙・斤量別の適切なテンションを探してもらいたい。
最後に裏技を紹介。
テンションを上げるとシワが発生、下げると紙が蛇行して見当がズレる。そんな、うまくバランスが取れない状態になった時は(薄紙でなりやすい)、シワが発生している箇所のガイドローラー端にテフロンテープやガムテープを巻いてもらいたい。そうすることで紙の張り具合が安定し、多少テンションを高めにしてもシワが発生し難くなる場合もある。一度試してみて下さい。 |
|
|
|
|
 |
No.013 |
スプレーパウダーの選定方法 |
2008/02 |
|
|
油性の枚葉印刷では、裏移りやブロッキングを防止するためにスプレーパウダーを印刷物に吹き付ける必要がある。油性インキの乾燥方式は酸化重合型と呼ばれ、空気と触れることによって乾燥する仕組みになっている。パウダーの役割は、積み重ねられた印刷物の間に入り込み、空気の流れる隙間を作り出す事でインキの乾燥を促進させる事である。
パウダーには様々な種類があるが、選定のポイントは大きく分けて2つある。
1 つ目のポイントは粒子サイズ。粒子サイズは一般的に15μから50μまであり、最適なサイズの選択は使用する用紙の厚みによって考えると良い。例えば、0.1mm以下の用紙をメインに印刷するのであれば15μ。0.2mm位までの紙を印刷するのならば20μがベスト。 それよりも厚い紙ならば30μ以上のパウダーを選ぶことで裏移りのトラブルを未然に防ぐ事が出来る。
基本的には、薄い紙には細かな粒子、厚い紙には粗い粒子を使用すべきだが、粒子が粗くなるに連れて表面のザラザラ感が残りやすいので、品質が重要視される印刷物にはなるべく細かな粒子を選ぶと良い。という事で、パウダーの粒子サイズは用紙の厚みを基準にして、用紙の種類や印刷絵柄を考慮して微調整する事をお勧めする。
2 つ目の選定ポイントはパウダーの表面加工の有無。パウダーは主にコートタイプ(撥水型)とノンコートタイプ(親水型)に分かれ、コートタイプは水に溶けにくく、ノンコートタイプは水に溶けやすい特徴を持つ。現在使用しているパウダーがどちらのタイプか分からなければ、コップの水にパウダーを入れるとすぐに判断が出来る。コートタイプは水の上に浮いたままの状態だが、ノンコートタイプはすぐに溶けて無くなってしまう。
この水との相性はブランケット残りとデリバリー上に溜まったパウダーに大きく影響するので覚えておいてほしい。 片面機で両面の印刷を行うには印刷機を2回通す必要があり、裏面の印刷を行う時には先行面を刷った時に付着したパウダーがブランケットに残ってしまう。この時、ノンコートタイプのパウダーを使用すると版からブランケットへと伝わる湿し水がパウダーを溶かしてくれブラン残りの発生を抑えるが、コートタイプのパウダーは水に溶けないので、そのままブランケットに残ってしまう。
またデリバリー上に溜まったパウダーは湿気との関係が深く、ノンコートタイプのパウダーは湿気の影響から固まりやすく、しばしばボタ落ちの事故を発生させてしまう。それに対して、コートタイプのパウダーは湿気の影響はほとんど受けず、デリバリー上でも固まらず、ボタ落ち事故を発生させない。
コートタイプとノンコートタイプの選択は、使用印刷機と仕事内容によっておおまかに分かれる。例えば両面専用機であれば仕事のほとんどが1パスなので、ブラン残りの心配がなく、後はボタ落ちに注意すれば良い。という事で、コートタイプを選択することが正解。それとは逆に、片面機で常に2回通すような場合には、ブラン残りを極力無くすためにノンコートタイプをお薦めしたい。どちらを選ぶとしても、ボタ落ちに関しては小まめな清掃を行なう事で回避出来るので、ブラン残りの対策を優先に考えるべきだと思う。
どちらのタイプか選びきれないという場合は、中間の性能を持ったハーフコートタイプもお薦めである。これはパウダー表面の半分を撥水コートしたもので、空気中の湿気には強いが水そのものには弱い特徴を持っている。
以上のようにパウダーの選定には、粒子サイズと表面加工に注意して行なうことがトラブル軽減の近道となる。
弊社ではコートタイプ、ノンコートタイプ、ハーフコートタイプのパウダーを取り揃えており、パウダー関連のトラブルに対して的確なアドバイスと、印刷条件にマッチしたパウダーの選定をお手伝いしております。単に裏移り対策だけでなく、使用量の削減、さらには現場環境の改善までご協力させて頂きますので、質問等御座いましたらお気軽にお問い合わせください。 |
|
|
|
|
 |
No.012 |
色 |
2008/02 |
|
|
私たち印刷業界に携わっている中で、「色」という言葉は大変重要な要素の1つである事は言うまでもありません。
では、「色」とは一体どのように表現されているのでしょうか?印刷に於ける基本色はCMYK(シアン・マゼンダ・イエロー・ブラック)の4色で、それらを基に様々な色が再現がされています。また、テレビなどのモニターではRGB(レッド・グリーン・ブルー)の光の三原色による組み合わせで表現しています。
私たちが普段目にする印刷物の殆どはCMYKの4色から構成(最近では6色や7色も存在)されていますが、印刷の詳細を知らない人にとっては写真集等の雑誌がたったの4色で再現されているなんて信じられないことでしょう!現に私もこの業界に入るまでは知らなかった一人です。
そこで、今回は実際に色とはどれだけの種類が存在し、どう表現するかを簡単に説明したいと思います。例えば、誰もが学生時代に体験していると思いますが、「黄色」の絵の具と「青色」の絵の具を混ぜると理論上「緑色」になりますが、その割合によっては様々な緑色が無数に出来上がります。その出来上がった色を数値的に表す方法としてマンセル色体系という物があります。これはアメリカの美術教育者であるアルバート・マンセル(Albert H. Munsell、1858-1918)によって色という概念を系統的に扱うために作り出された物で、「マンセル表色系」あるいは「マンセル・カラー・システム」などとも言われています。
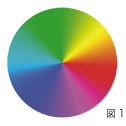
マンセル色体系では色の3属性は色相・明度・彩度とされており、色相は赤(R)、黄(Y)、緑(G)、青(B)、紫(P)の基本色と黄赤(YR)、黄緑(GY)、青緑(BG)、青紫(BP)、赤紫(RP)の中間色の合計10色に分割されています。(図1)
明度は最も明るい白を10、最も暗い黒を0として色の明るさを表し、彩度は色の無い無彩色を0として色の鮮やかさの度合いにより数字を大きくしていくことで色の鮮やかさを表します。
この3属性を含めて視覚的に図示したのが「マンセル色立体」と呼ばれるもので、地球儀のような球体の形をしています。(図2.3)
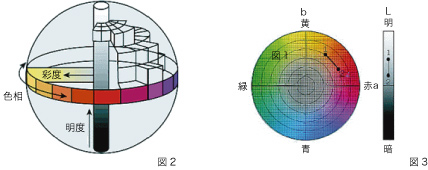
このように、決して色は感覚のみに従事するものではなく、属性を持つ、数値化可能な一つの表現要素と言えるのです。
印刷品質の管理手段の一つとして一昔前は主に濃度計が用いられていましたが、現在ではそれに加えて色彩計(分光測色計)等で管理する会社が増えてきています。これは図3にある様に横軸にa軸、縦軸にb軸、中心の前後にL軸を設定し、それぞれの値で色の数値化(Lab値と言います。)し、色の面から品質を徹底管理するのに優れています。
今まで皆さんの中にも印刷立会いなど経験で、「ちょっと色が違うんだよなぁ〜!もう少し赤味を抑えて!」と言われるような経験があったと思いますが、そういった個人個人の感覚における色の違いも色彩計を用いれば、きちんと数値で表す事ができ、その数値に忠実に再現することも可能なのです。
色々な絵の具を使って無数の色を作るのと同じで、印刷でも調整次第で様々な色を作り出す事が出来ます。そして、それぞれの色はきちんと数値化(Lab値)することも可能です。基本的には見本(原稿)に対して忠実に再現する事がプレスマンの役割、そして義務ですが、言い換えれば、自分の調整次第でどんな色にも表現し得るという面白さがあると思うのです。印刷の面白さ、プレスマンである事の面白さはそこにあるのかも知れません。
※引用図:フリー百科事典『ウィキペディア(Wikipedia)』より |
|
|
|
 |
No.011 |
工場緑化のすすめ |
2008/02 |
|
|
先日飛行機の機内誌でアル・ゴアの「不都合な真実」の翻訳をした環境ジャーナリストの枝廣淳子さんのレポートを読んだ。産業革命後の化石燃料(石油、石炭、天然ガス)の大量使用により、今日人類は大気中に年間72億トンの二酸化炭素を放出しており、地球の森林生態系と海洋が吸収出来る31億トンを大幅に上回り、自然のバランスを狂わしてしまっている。この余剰な二酸化炭素が大気中に溜まり、今日の地球温暖化の原因となっており、気温上昇以外にも、ハリケーンや台風の巨大化、北極やグリーンランド等の氷が溶け海面上昇が始まっている。地球温暖化により産業革命(一般的には1760年〜1830年)以前の温度より地球の平均温度が2℃高くなってしまうと、地球環境が急激に変わり、「飢餓が増える」「マラリアが増える」「水不足が広がる」等の問題に繋がってしまう。この100年で地球の温度は既に0.74℃上がってしまっているので、残りの約1.3℃上昇を防ぐために、人類は大きな方向転換をしなければならないという趣旨のレポートだった。
我々印刷業界も、地球温暖化には遠かれ少なかれ影響を及ぼしていると思う。
印刷現場では石油ベースの諸材料を使用しているし、電気は大量に使っているし、地球の樹木を伐採して、それを用紙にして印刷を行っている。いわば、二酸化炭素を大量に発生しつつ、二酸化炭素を吸収してくれる木に印刷を行っているといった具合だ。
それに対して印刷業界は何をすべきか?
自分は一つのアイデアとして、工場の緑化を提案したい。
日本全国の印刷工場の屋根を緑化し、壁面を緑化し、駐車場を芝生に出来たら、緑が二酸化炭素をどんどん吸収してくれる。印刷工場全体を環境仕様にしてしまえ!というアイデアだ。
早速昨年から緑化を勉強して、屋上緑化から壁面緑化まで日本にある緑化方法は全て提案出来る体制を整えつつある。
これに賛同して下さる方がいる場合は、ご一報下さい。御社の予算に合った最適な工場緑化を実現致します。 |
|
|
|
|
 |
No.010 |
「PRTR」について
|
2008/02 |
|
|
基本的なところから復習するつもりで、化学物質に関連する法規制、制度について、先ずは「PRTR」について説明したいと思います。
環境中に排出された化学物質、例えば農薬などは、害虫駆除などのメリットと、使いすぎると人の健康や生態系に有害な影響与えるデメリットの両面性を持っています。このデメリットを「環境リスク」といいます。
このメリットとデメリットのバランスを考えながら「環境リスク」が小さくなるように化学物質を使用することを、「リスク管理」といいます。また、大勢でリスク管理を考えることを「リスクコミュニケーション」といいます。
PRTR(Pollutant Release and Transfer Register:化学物質排出移動量届出制度)とはリスクコミュニケーションの道具として制度化されたもので、「使用してはいけない」などの規制的な性格はもっていません。環境リスクを持つ化学物質(435種を指定)の排出削減に取り組んでいくためには、その出発点として、どのような化学物質が、どこから、どのくらい、環境(大気・水域・土壌など)中へ排出されているか(排出量)、廃棄物などとして移動しているか(移動量)を把握し、基本的な情報をすべての関係者に開示、共有することにより、市民の監視のもと企業の自主的な削減努力を促すことを目的としています。企業の排出・移動量は、自ら調査・把握して都道府県に届け出ることになっていて、排出・移動量を把握する方法は国によってマニュアルが作成されています。
合理性のある制度と思われますが、いくつかの問題もあります。
- 都道府県に届けられて、開示対象とされるのは、最終的な集計結果の数値(俳出、移動量)だけで、企業ごとの数値は開示請求しなければ入手出来ない。
- 数値の検証を行うことは難しい。
- 把握されるのは「排出量」、「移動量」だけであり、「使用量」については把握されない。
- 年間1トン(発がん性のある12物質については0.5トン)以上取り扱う事業者に課せられ、小規模事業者や家庭からの排出については免除されている。
- 合成洗剤(合成界面活性剤)などの有害化学物質が家庭から排出されている。
これらの諸問題はあるものの、PRTRのそもそもの目的である「リスクコミュニケーション」については企業として率先して行うべきだと考えます。
弊社としましては、PRTRで指定された435種を含めて、公的に環境リスクが明らかになった化合物については率先して使用削減または停止をして、「環境リスク」の小さい化学物質での製品開発を追求して行きたいと思います。 |
|
|
|
|
 |
No.009 |
静電気 |
2008/01 |
|
|
私は枚葉印刷のオペレーターを9年間経験しましたが、毎年冬場になると静電気に悩まされていた事を思い出します。今では印刷資材を売る営業として日本全国の印刷会社を訪問していますが、多くの印刷会社が冬の静電気には苦労をしています。
静電気のトラブルとして一番に挙げられるのが給紙または排紙不良。これは作業時間のロスに繋がり、酷い時には用紙が不足してしまう事もあります。経験豊富なオペレーターはどうにかそれを扱うことも出来ますが、冬場の静電気は現場の大きな負担となっている事には間違いありません。
「そんな静電気の軽減方法は?」と聞かれると、自分は「まずは加湿コントロールです!」と答えています。
印刷現場の適正な湿度は55%前後で、現場がこの適正値をキープしているかの小まめなチェックが大切。いわば「湿度の見える化」が重要になります。適正値がキープ出来ている場合はそれ以上の加湿は無用。湿度を上げれば上げるほど静電気の発生は無くなりますが、インキの性質の変化や機械の腐食等の弊害が発生してしまうので、やりすぎには注意が必要。もし、湿度が適正値よりも大きく下回っているのならば、加湿器の整備や出入り口を2重シャッターにするなどの改善が必要となります。
もし加湿器の設置等の多額の費用をかけずに静電気を解決したい。または、フィルム等の印刷で適正湿度の環境下でも静電気が発生してしまうという場合は、除電効果のあるロープの設置をお勧めします。
弊社は静電気を解決する為の加湿器から除電ロープまで様々な商品を取り揃えております。湿度の見える化には「デジタル温湿度計」がピッタリですし、安く静電気を解決したい場合は、「静電防止ロープ」シリーズをお勧めします。
製品の正しい設置方法もアドバイス致しますので、静電気にお困りの場合は、是非ご一報下さい。
電話:03-3856-5111
mail:kiryu@sk-liquid.com |
|
|
|
|
 |
No.008 |
24時間体制と賃金 |
2008/01 |
|
|
現在、オフ輪の印刷会社は24時間作業を実施しているところが多い。
これはオフ輪印刷機が「大ロット」「短納期」に対応していることが、大きな要因の一つになっており、例えば数百万部という印刷物を数日で納品しなければならないのだから、夜中であっても機械を停止させるわけにはいかないのである。
24時間勤務は概ね、2交代制か3交代制のどちらかが選ばれている。
早番(例・8時〜20時)と遅番(20時〜8時)が1週間ごとに入れ替わるのが2交代制。一方、3交代制は2日ごと(会社によっては3日ごと)に入れ替わる。『早番を2日間_遅番を2日間_休日2日間_早番に戻る』といった具合だ。自分はどちらも経験したが、正直、労働条件としては良いものではなく、これが若手オペレーターの職離れの一因となっている。
先日、知り合いの若いオフ輪オペレーターが職を離れた。
3交代制で働いていた彼の月給は、手取りで15万円以下だったそうである。土日関係なく夜勤もこなしながら数年頑張っていたが、賃金が労働条件に見合わずとても続けられないと判断したようだ。
前回のコラムと重複するが、現在、印刷会社の多くは、人員(特に若手オペレーター)の確保に四苦八苦している現状がある。高齢化社会の時代に突入し、この問題はさらに深刻化していくだろう。
CMS(カラーマネージメントシステム)など印刷品質の強化を計り、その為の設備投資を行なう印刷会社は増えているが、従業員の給与を(上げる方向で)見直す会社の話は聞いたことがない。勿論、支払いたくても支払えない事情もあるかとは思うが、それは印刷単価の低価格競争が招いた結果でもある。
単価を下げ仕事を確保出来たとしても、人員がいなければ印刷機を稼働させることは出来ない。そういった当たり前のことを、もう1度認識しなければならないのではないだろうか。 |
|
|
|
|
 |
No.007 |
インラインコーター |
2008/01 |
|
|
最近、印刷展示会や業界紙などで「インラインコーター」という言葉を良く耳にすると思うが、これは印刷ユニットとは別にニスの専用ユニットが有り、印刷と同時にニス引き加工をインラインで作業できる事を意味する。
ニス引きを行う理由としては印刷表面を保護する事が目的とされ通常のユニットを利用してのOPニスと専用コーターを用いる物の2つに別れる。元々、インラインコーターを導入する印刷会社の多くはパッケージを主体とした印刷会社が多く、IRシステム(赤外線乾燥)との組み合わせで、厚紙でも棒積みが可能となり作業性が大幅にUPした。しかし、ここ数年はUV乾燥システムとの併用で様々な付加価値印刷が可能となった事でパッケージ印刷以外にも一般商業印刷分野でもインラインコーターが装備された印刷機が数多く導入されている。付加価値印刷の例を挙げると、
- 擬似エンボス加工
- スクラッチ印刷
- 圧着ニス加工
- 光沢スポットニス
などが有る。
コーターシステムとしてはロールコーターとチャンバーシステムが有り、現在はアニロックスローラーを使ったチャンバーシステムが主流となっている。ロールコーターは簡単に言うと連続給水システムと似ており、元ローラーの回転量によってニスの塗布量を増減できる。しかし、天地によっての塗布量が均一にならない欠点がある。その点、アニロックスローラーはローラー表面に彫刻加工を施しセル容積を形成させてニスを塗布させるため、印刷全体を均一な皮膜で管理する事が可能となり、現在はこちらが主流となっている。しかし、塗布量を変化させるためにはセル容積の違ったローラーに替えなければならない事がある。
このようなインラインコーターを使う事によって、印刷直後でも後加工が可能となり生産性をUPさせたり、他社では出来ない付加価値印刷で差別化を図る事によって、決して成長産業とは言えない厳しい印刷業界の中で、受注を増やす会社も数多く有る。
弊社ではこのようなインラインコーターで使われる資材(コーター版・ブランケット・洗浄剤等)も数多く取り揃えており、他社との差別化を図る印刷会社をバックアップしています。 |
|
|
|
|
 |
No.006 |
印刷機1オペレーター時代の到来? |
2008/01 |
|
|
昨年の6月に仕事でデンマークに行った。デンマークの印刷資材メーカーとの商談がメインだったが、そのついでに現地の印刷会社も見学させて貰った。驚いた事が、日本では通常2人で印刷を行う菊全の4色機、5色機をデンマークでは1人で印刷をしている点。社会福祉の国、デンマークでは税金ががとても高く、人件費が馬鹿にならないので、ずいぶん前から印刷機は1人で回すというのが当たり前だそうだ。
そのデンマークの取引先の人間に、「デンマークでオペレーター1人の月の人件費はどれだけかかるの?」と聞くと、「日本円で60万円以上はするでしょ」との事。「ひえー」である。
話はアジアに飛び、弊社は昨年、中国の大連に支社を設立し営業活動を開始している。人件費が月2万円程度の中国では、1台の印刷機にオペレーターが1人、アシスタントが3人いるので、デンマークとの差に笑ってしまったことがある。しかし、中国は別の事情があり、オペレーターがどんどん給与の高い会社に移籍してしまう為に、印刷会社は常にスペアの人材を育てる必要があり、1台の印刷機を4人で回しているという背景もあるようだ。
中国の人件費の安さは公然の事実だが、デンマークの人件費の高さはあまり知られておらず、今回のコラムを書く上で是非とも裏付けが欲しかった。インターネットで調べたところ、総務省の「世界の統計2007」という資料にたどり着いた。このデータには各国の平均賃金が報告されており、日本は最新情報が2005年調べで平均賃金は月 292,100円。中国は23,131円。そしてデンマークは驚きの671,440円である。しかし、この所得に対して国税と地方税で平均69%が国庫に収まり、消費税も25%である。67万円の約3割=約20万円が手元に残るという事で納得できる数字だが、この高賃金を支払う経営者にとってはたまらない。印刷機を1人で回そうと考えるのも理解出来る。
さて、話を戻し日本の印刷業界。相も変わらずの低価格競争で印刷単価の下落は進んでいる上、印刷用紙やインキ等の諸材料は値上がるという大変な状況に置かれている。そんな中での経営判断の1つとして北欧型の印刷機を1人で回すというスタイルに移行し、販売管理費の削減を目指す事もありだと思う。
弊社では印刷機を1人で回す、1人でメンテナンスをするのに適した商品も取り揃えているので、興味のある場合は営業スタッフに相談して頂きたい。 |
|
|
|
|
 |
No.005 |
洗浄剤について |
2007/12 |
|
|
オフセット印刷で用いられるインキを成分で大きく分けると、「顔料成分」と「ビヒクル成分」に分けられます。顔料成分は色材としての働きを持ち、ビヒクル成分は様々な樹脂、植物乾性油、鉱物油、高沸点・低沸点溶剤、ワックスから成るもので、顔料を分散させたり、インキ壷から版、紙などの素材へスムーズに移動させる「膜」となって顔料を固着させるなどの働きを持ちます。 いずれの成分も水に溶けないので、洗浄するには主成分として溶剤が必要になります。
溶剤として以前から用いられてきた、石油系芳香族炭化水素成分(アロマ)、揮発性有機成分(VOC)は中核神経や腎臓及び肝臓への機能障害を誘引したり、麻酔作用や皮膚・粘膜刺激作用を起こすため、作業安全性や大気汚染防止の観点から、代替成分への移行や削減が進んでいます。
代替成分として、揮発性の低い石油系肪族炭化水素(ナフテン系、パラフィン系)が実用段階に入っており、植物由来の炭化水素、脂肪酸エステルも検討が進んでいますが、コストが上がってしまう事と、溶剤の乾燥性が悪くなり、から拭きや水拭きといった一工程が増えて作業効率が悪くなってしまう事が普及を遅らせているようです。
化学物質の環境、及び人害リスク管理も様々な法規制を通して進んでいますが、現実的には作業安全性や大気汚染防止と同様に、コストや作業性もクリアしないと、普及していかないのが現状だと思います。そのことを踏まえると、洗浄剤を供給する側として、ユーザーにハードルの高い規制への理解を呼びかけるだけでなく、『需要者各現場に即したレベルアッププラン』、『環境・人害リスクの段階的な軽減の説明』、明らかにリスクの高い化合物の使用を除く『各段階に対応するベストな洗浄剤の設計』を提示していく必要があると思います。
当社としましても、まだまだユーザーの皆様に納得の行くプランを用意できていないのが現実。2008年は少しでも前進できるよう努力したいと思います。 |
|
|
|
|
 |
No.004 |
オフ輪の印刷単価 |
2007/12 |
|
|
現在、印刷料金は年々下落傾向にあり、特に顕著なのがオフ輪の印刷単価です。
印刷料金は1色=○銭と決めるのが通例で、これを印刷単価と言います。表4色+裏4色=8色なので、例えば1色16銭の契約ならば、印刷物1部の印刷料金は16×8=128、つまり1円28銭となります。オフ輪で最も普及しているB縦半裁機の紙サイズは概ね765mm×546mm。そのサイズを1部印刷して1円28銭の料金となるわけです。
さて、その印刷単価ですが、1色12銭が採算の合うラインと言われていました。1部にすると96銭。ほぼ1円です。1円を切ったら儲けが出ず、何かミスでも出して巻取り(紙)を買い足すなどしたらもう赤字決定とも言われていました。ところが最近、1色6銭(1部=48銭)まで印刷単価を下げている会社があると耳にしました。採算が合うのか外部からはわかりませんが、そこまで下げても仕事を確保したいというのが実情のようです。
当然、その皴寄せは現場のオペレーターに来ます。賞与・給与のカット、人員の削減などなど。一昔前まで3〜4人で1台の機械を廻していましたが、現在は2人が主流になり、もっと過激な会社は1.5人体制(機械2台に3人)を取るところもあります。つまり仕事はキツくなったのに収入は減ったということです。結果として若手オペレーターの多くが、職を離れてしまい、多くのオフ輪会社では【現場の若返りを進めたいのに慢性的な人員不足】という現象が起きているようです。
今年に入り印刷材料のメインである「紙」と「インキ」の価格が上がりました。こうなると印刷会社の利益幅はさらに狭まり、その皴寄せがまた従業員に波及するでしょう。
この現状を克服する為には、印刷単価を上げる事が必須になり、色々な会社が現在模索中の状態です。以前はオフ輪そのものが、「枚葉機の数倍のスピードで印刷を行い、大ロット・短納期を実現する」という付加価値印刷でしたが、市場に印刷機が1000台以上もある今日では、各社が少ない仕事のパイを低価格で奪い合っている現状になっています。折り加工等の後加工で差別化を図ろうとしている会社もありますが、実際のところ格段に利益が上がる程でもないようです。
という事で、オフ輪印刷の単価を上げるという課題は、なかなか結論を出すのが難しい問題だと思います。しかし、印刷会社としての利益を守り、将来の担い手になる若手オペレーターを今後も育成・確保する為には、例えば、大手インキメーカーが足並みを揃えて値上げを行ったように、オフ輪業界全体も一丸となって取り組んで欲しいと、私個人は考えています。
先日聞いたあるオペレーターの言葉が印象的でした。彼は自分が刷った印刷物(チラシ)を拡げ、こう言いました。
「これだけ頑張って仕事しても、このチラシが1円にもならないんです。やる気を失くしそうですよ」 |
|
|
|
|
 |
No.003 |
色 |
2007/12 |
|
|
印刷現場には、数ある色を上手に組み合わせクライアントの希望する色を出すことが求められる。クライアントの希望に沿った色を出せる印刷会社こそが、より多くの受注を得ることが出来る。
しかし、色というのは何も印刷物だけに限ったことでは無く、印刷会社自体もそれぞれ異なった色を持っている。それは各会社の経営方針や企業理念、会社の体質などで大きく分かれるのだが、その影響はとても大きく、現場の方の技術レベルや考え方、さらには人間性をも左右してしまう。
現場で働く方の大半は学校を卒業して印刷会社に就職する。印刷はもちろん、社会の常識も現場の環境の中で学んでいくのだから当然と言えば当然の事だと思う。言わば、その会社の常識が世間の常識となってしまう。
そのような状況が起きてしまう理由は、印刷会社同士の横の繋がりが少ないからである。とは言え、会社のトップに立つ方であれば他の印刷会社へ見学に行ったり情報交換をする機会も多い。そしてたくさんの刺激を受けて自社に戻り、社員にこのような指示を出す。
「A社の現場はもっと綺麗だぞ!もっと整理整頓をしなさい!」
「A社のようにやり方を変えて生産性を上げなさい!」
しかし、自社の常識しか知らない現場の方にそのような声は届かない。目で見て印刷物を確認する印刷オペレーターにとっては、実際に見てもいない事を実践しようとは思わない。
さらに、印刷では頻繁に慢性的なトラブルが発生する。そんな時に「他の会社ではどうやって解決しているのだろう?」と考えた事があるオペレーターは少なくないはず。しかし、他の会社のやり方を聞く術はないので自社の常識の範囲内で解決するしかない。
このような状況を打破するためには、現場の方同士での情報交換の場が必要となり、自分の目で様々な物を見て確かめて、現場のレベルアップを図らなければならない。そして、今まで持っていた自社の色と新たに手に入れた他社の色を混ぜ合わせ、クライアントの求める色を造り続けなければならない。
「オフセット印刷.net」がそんな交流の場になることを望んでいます。 |
|
|
|
 |
No.002 |
印刷技能オリンピック |
2007/11 |
|
|
「技能オリンピック」というイベントをご存知でしょうか?
2007年ユニバーサル技能五輪国際大会(通称:技能オリンピック)が先週静岡県で開催され、世界62ヶ国から3,700名強の参加者が集まり、48の職種で技能が競われました。第39回となる今大会では、印刷競技もその中に含まれ、微力ながら弊社もこの競技で使われる印刷資材の一部を提供させて頂きました。この技能オリンピックの歴史を調べてみると、以下の情報が静岡県のHPに掲載されていました。
『簡単にこの技能五輪の歴史を振り返ると、1950年にスペインとポルトガルとの間で技能の競技大会が開催され、これが第1回目の大会になりました。1966 年には参加国の代表により国際職業訓練機構が組織され、この組織委員会の定めた規約に基づき大会が運営され今日に至っています。
日本でも過去に、1970年第19回東京(千葉)大会、1985年第28回大阪大会の2回が開催され、今年が日本国内3回目の国際大会(2年に1度の開催)となりました。
大会趣旨は世界各国・地域の予選会を勝ち抜いた22歳以下の青年技能者が、国際大会の場でそれぞれの技能を競います。また大会を通じて参加国の職業訓練の振興及び技能水準の向上を図るとともに、国際交流と親善を目的としています。』*静岡県HP(技能五輪国際大会紹介)より抜粋
さて、注目の印刷競技は4色印刷で進められました。具体的な内容は3種類以上の用紙を使って、4種類の印刷作業を行い、時間内に規定の枚数を印刷するというもの。見本を忠実に再現することは勿論、印刷後、支給の濃度計を使用して濃度偏差(ドライダウン)、ドットゲイン(網点の大小変動)を測定しグラフ化することで、作品の印刷物と見本との変動を数字化で比較し品質チェックするという、高度な技術が求められました。
今回の印刷競技の結果は金賞がフランス、銀賞がスイス、銅賞がニュージーランド。日本代表は残念ながら6位で敢闘賞という結果でしたが、日本の印刷技術の高さを十分世界にアピールできたと思います。心より健闘を称えたいと思います。
私自身も長く印刷会社に勤務し、印刷を経験してきましたが、残念ながら当時は印刷競技が種目として存在していませんでした。そして種目が存在する今では、当然のことながら参加資格の年齢を遥かに超えているので参加は無理。残念!
技能五輪が存在するのだから、技能ワールドカップも存在しても良いのではないか?
技能ワールドカップの開催を思い描きつつ、日本の印刷技術における今後の発展に弊社が少しでも力添えできたら、と願うばかりです。 |
|
|
|
|
 |
No.001 |
時代はポストプレスへ |
2007/11 |
|
|
ご存知の通り、日本の人口は2004年12月の1億2783万8000人でピークを過ぎて(2006年12月27日読売新聞より)、これから日本は人口減少時代に突入する。国立社会保障・人口問題研究所『日本の将来推計人口(平成18年12月推計)』によるデータでは、日本の人口は今後50年間で 3000 万人減って、9000万人弱まで減少するそうだ。人口が30%近くも少なくなってしまうという事は、すなわち国内市場が小さくなるという事で、印刷業界を含めた日本の多くの産業が既にピークを過ぎた減少マーケットに突入している。既に毎年減少傾向にある仕事量を各社ひっきりなしに取り合っており、それが印刷単価の下落という形になってしまっている。
誰もが分かるとおり、このまま印刷単価が下がり続けたら、体力のない企業は徐々に倒産や廃業に追いやられ、最後には体力のある中堅〜大手企業が残るという筋道が出来ている。しかし、小さいなりにもキラッと光る独自のノウハウがある会社はこの時代も生き延びることが出来るだろう。そんな独自のノウハウを持っているか、持っていないかが多くの印刷企業にとってこれからの勝負になると思う。
この独自のノウハウは機械メーカーが推奨する新機能を購入するだけでは足りないと思う。先日業界新聞である印刷機メーカーの新機能フェアーに1000人を超える参加者があったそうだ。どんなに新しい機能でも100社も200社もそれを採用してしまったら、独自性はなくなるというものだ。やはり目指すレベルは会社独自の特殊印刷を考え出して、それでパテントを取る位のものであろう。
印刷はプリプレス、プレス、ポストプレスに別けられるが、プリプレスとプレスに独自のノウハウを持つのは難しい。高級印刷などと謳っても、すでに高級印刷 は当たり前の世界なので、プレスで差別化を行うのも至難の技だ。という事で、時代はポストプレスに流れつつある。 |
|
|
|
|